
Effect of limestone and dolomite flux on the quality of
The particle size distribution of the iron ore fines is presented in Fig. 1. It indicates that more than 65% of the particles are below 45 μm. Blaine number of iron ore fines was measured as 2920/cm 2.g −1. It illustrates that the particle size distribution and Effect of limestone and dolomite flux on the quality of ,The present work illustrates the effect of limestone and dolomite as flux material in pelletization of an Indian goethetichematite iron ore The proportion of Iron Ore Pelletizing Process: An Overview,The iron ore production has significantly expanded in recent years, owing to increasing steel demands in developing countries.

(PDF) Iron Ore Pelletizing Process: An Overview
Iron ore fines generated from the beneficiation process cannot be used directly in blast furnaces for steel making. known as Fruitful role of dolomite in pelletization of iron ore fines ,Contribute to changjiangsx/Fruitful development by creating an account on GitHub.Strengthening pelletization of manganese ore fines ,Pelletization is one of useful processes for the agglomeration of iron ore or concentrates. However, manganese ore fines are mainly agglomerated by sintering due

Pelletization Fruitful Outotec
Parts and services. Pelletization is the process of transforming iron ore fines into spherical pellets through agglomeration and induration. These pellets are then used as feed to a role of dolomite in pelletization of iron ore fines,68 HighLOI iron ore fines are required for detailed laboratory pelletization studies and are used in pellet making. The received iron ore is martite–goethitic and role of dolomite in pelletization of iron ore fines,iron ore pelletization plant. A Look at the Process of Pelletizing Iron Ore . Pelletizing, or balling, carried out through either a disc pelletizer or rotary drum, is a key
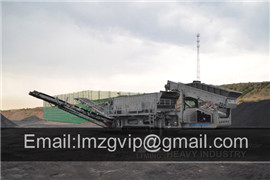
Role Of Dolomite In Pelletization Of Iron Ore Fines
Beneficiation Low Grade Iron Ore Fines Grinding. Nioshtic2 Publications Search 10002890 Beneficiation. 10002890. Abstract.(PDF) Iron Ore Pelletizing Process: An Overview,Iron ore fines generated from the beneficiation process cannot be used directly in blast furnaces for steel making. known as iron ore pellets [2]. Hence, pelletization, the process of pelletIron ore pelletizing Fruitful Outotec,Iron Ore Pellets are formed from beneficiated or run of mine iron fines. The iron is usually ground to a very fine level and mixed with limestone or dolomite as a fluxing agent and bentonite or organic binders as a binding

Innovative Development on Agglomeration of Iron Ore
ABSTRACT In steel industry and in mines, a significant amount of ultrafines waste iron oxides and iron ore fines is generated. Utilizations of these fines are required to reduce the environmental hazards and conserve the natural resources. Some of these fines are normally used in sintering practice. However, sintering has a limitation of Iron Ore Pelletization Technology and its Environmental ,lumps in total iron ore production has been about 40 % with the rest being accounted for fines and concentrates. Iron Ore Fines/blue dust cannot be charged in the blast furnace directly since they block the passage for ascending gas inside the feed. Moreover, the excessive fines generated from the iron ore crushing units are mostly Effect of Blaine Fineness on the Quality of Hematite Iron ,Iron ore pellets are largely characterized by inherent physical and chemical properties of ore as well as pelletizing conditions including induration time, induration temperature, etc. These parameters essentially vary with types of ores. The production of highquality pellets from hematite ore is challenging because of high level of fineness (Blaine number) and
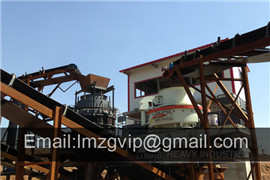
Gratekiln pelletization of Indian hematite fines and its
Indian hematite fines normally have a high iron grade and minor impurities; they are usually used as sinter fines for feeding into a blast furnace. In this work, the grindability properties of two kinds of Indian hematite fines and the roasting behaviors and induration characteristics of pellets made from these fines were revealed through Pelletization of iron ores and the type of wear ,The “pellets” or “Iron ore pellets” is actually a spherical uniform form of iron ore fines mixed with some ingredients like Dolomite, Bentonite, limestone and coke breeze which are later introduce in a Research Progress of Intelligent Ore Blending Model,The iron and steel industry has made an important contribution to China’s economic development, and sinter accounts for 70–80% of the blast furnace feed charge. However, the average grade of domestic iron ore is low, and imported iron ore is easily affected by transportation and price. The intelligent ore blending model

Attrition characteristics of limestone in gassolid fluidized
The attrition mill (Fig. 1), based on Gwyn's design, consists of a 25.4 mm 316SS cup with interchangeable 6.4 mm thick metal disks with a single orifice in the center (0.39 mm) connected to air supply system .The orifice extended from the bottom of the disk to the bottom of the “shroud” (3.0 mm). The length of the cup above the orifice plate was REDUCED IRON MANUFACTURING METHOD AND ,1. A method of producing reduced iron from fine iron oxides,comprising the following step of a) through c): a) obtaining raw material mixture by mixing fine iron oxides and powdery solid reductants; b) forming a bed of substantially uniform thickness on the hearth of a reduction furnace by charging the raw material mixture in the form of fines into the reduction Iron Ore Pelletization: Part I. Fundamentals: Mineral ,ABSTRACT. The behavior of iron ore pellet binders is complex. Any pellet binder is subject to a handful of practical requirements: that it be readily dispersed through a pellet, that it effectively controls the movement of water within the pellet, and that it contributes to the interparticle bonding within the pellet.
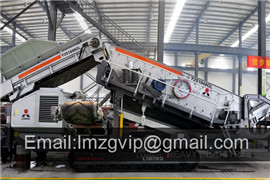
Usage of HighLOI Iron Ore Fines in Pellet Making
HighLOI iron ore fines are required for detailed laboratory pelletization studies and are used in pellet making. The received iron ore is martite–goethitic and hematite–goethitic form of ore with high LOI content. The iron ore consists of 57.7% Fe, 6.19% SiO2, 2.69% Al2O3, 8.80% moisture and 8.85% LOI. From thermogravimetric Influence of flux additives on iron ore oxidized pellets,Six additives, i.e., limestone, lime, magnesite, magnesia, dolomite and lightburneddolomite, were added for investigating their influences on the pellet quality. For green balls, adding lime and lightburneddolomite makes the wet drop strength decrease firstly, and then increase with further increase of additive dosage. Ca(OH)2 affects the (PDF) Evolution of the flux combination for pelletization of ,[Show full abstract] effect of limestone and dolomite as flux material in pelletization of an Indian goethetichematite iron ore with 59.75% Fe, 4.52% SiO2, 3.84% Al2O3, and 4.85% LOI. As per

Recycling and Reuse of Iron Ore Pellet Fines SpringerLink
For pelletization study, as received iron oxide pellet fines were ground to below 150 μ using ball mill. The particle size distribution of ground iron ore fines was determined by the Malvern particle size analyzer (Hydro 2000MU, UK) and shown in Fig. 2.Blaine number was measured to determine surface area of the iron oxide pellet fines Effect of Blaine Fineness on the Quality of Hematite Iron ,Iron ore pellets are largely characterized by inherent physical and chemical properties of ore as well as pelletizing conditions including induration time, induration temperature, etc. These parameters essentially vary with types of ores. The production of highquality pellets from hematite ore is challenging because of high level of fineness (Blaine number) and EFFECT OF SIZE DISTRIBUTION AND WATER CONTENT ,India has about 28.5 billion tonnes of Iron ore reserves. However, almost 60% of the ore that is mined is in the form of fines of low iron content. These iron ore fines cannot be directly used in the blast furnace as they pose the following threats: 1. Iron ore fines severely reduced the permeability of the bed, jeopardizing
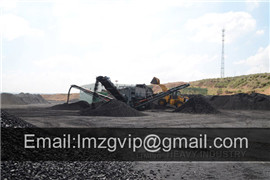
Role Of Dolomite In Pelletization Of Iron Ore Fines
Beneficiation Low Grade Iron Ore Fines Grinding. Nioshtic2 Publications Search 10002890 Beneficiation. 10002890. Abstract.Innovative Development on Agglomeration of Iron Ore ,ABSTRACT In steel industry and in mines, a significant amount of ultrafines waste iron oxides and iron ore fines is generated. Utilizations of these fines are required to reduce the environmental hazards and conserve the natural resources. Some of these fines are normally used in sintering practice. However, sintering has a limitation of Attrition characteristics of limestone in gassolid fluidized ,The attrition mill (Fig. 1), based on Gwyn's design, consists of a 25.4 mm 316SS cup with interchangeable 6.4 mm thick metal disks with a single orifice in the center (0.39 mm) connected to air supply system .The orifice extended from the bottom of the disk to the bottom of the “shroud” (3.0 mm). The length of the cup above the orifice plate was