
Ball Mill Design/Power Calculation Mineral
The basic parameters used in ball mill design (power calculations), rod mill or any tumbling mill sizing are; material to be Ball Mill an overview ScienceDirect Topics,Conical Ball Mills differ in mill body construction, which is composed of two cones and a short cylindrical part located between them (Fig. 2.12).Such a ball mill body is expedient Ball mill media optimization Metcom Tech,torque mill test is the mill energy input divided by the solids load. The energy specific cumulative grinding rate at each screen size is calculated from a torque
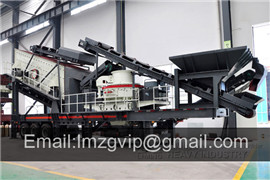
Mining Engineering 1957 Vol. IX Metallurgist & Mineral
In this formula B is the diameter of the ball to be charged, in inches; C is the percent critical speed of mill; D is the inside mill diameter, in feet; F is the size of Choosing the correct mill screen for your bulk ,Round Hole Cone Mill screen. The round hole screen is widely used for conical milling applications. It is typically used for dry milling, blending, deagglomeration and for reducing the bulk density of spray Ball Mills Mineral Processing & Metallurgy,CERAMIC LINED BALL MILL. Ball Mills can be supplied with either ceramic or rubber linings for wet or dry grinding, for continuous or batch type operation, in sizes from 15″ x 21″ to 8′ x 12′. High density

Ball Mill Parameter Selection & Calculation JXSC
1 Calculation of ball mill capacity. The production capacity of the ball mill is determined by the amount of material required to be ground, and it must have a certain Design and Analysis of Ball Mill For Paint Industries IJSRD,can reducing running cost of ball mill. Optimizing is done by Modeling and Analysis of parts of ball mill by using ‘Finite Element Method’. Keywords:Parameters, Ball Mill Discharge Spiral and Trommel Screen,The Ball Mill Discharge Spiral Screen is designed to make a sized product, particularly for “SubA” Unit Flotation Cells and concentrating tables. It is also used to screen out and return to the ball
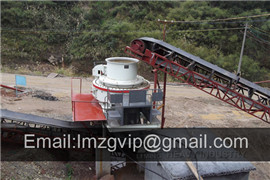
17 Signs of Problems with Ball Mills: Quickly Remove
High temperature of the ball mill will affact the efficiency. 3 For every 1% increase in moisture, the output of the ball mill will be reduced by 8% 10%. 4 when the (PDF) Design of Threechamber Ball Mill ResearchGate,3.5 × 13m threechamber ball mill pitch diameter of the mill taken 4 times. 𝑙 4D 14 m ( 2 ) The turning of the ball mill refers to the turning of the barrel of the ball mill when it is workingBall Mill an overview ScienceDirect Topics,Conical Ball Mills differ in mill body construction, which is composed of two cones and a short cylindrical part located between them (Fig. 2.12).Such a ball mill body is expedient because efficiency is appreciably increased. Peripheral velocity along the conical drum scales down in the direction from the cylindrical part to the discharge outlet; the helix
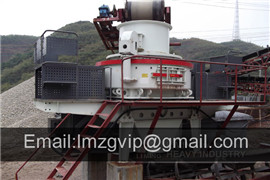
Particle size reduction, screening and size analysis
walls as seen in figure 1. A variation is a jar mill, in which relatively small ceramic containers holding some grinding media are rotated on a common machine frame. It is used for small batches of valuable chemicals and in laboratories. Figure 1. Schematic representation of the crushing mechanism in a ball millBall Mills Industry Grinder for Mineral Processing JXSC ,Ball Mills Capacity】 0.290 T/H Advantages】Designed for long service life, minimum maintenance, can grind and homogenize mineral ores down to the nano range, a large volume of processing capacity Max Feeding Size】 <25mm Discharge Size】0.0750.4mm Types】Overflow ball mills, grate discharge ball mills Service】 24hrs The Effect of Ball Size Diameter on Milling Performance,A laboratory size ball mill of diameter 30 cm was used with ball media of sizes 10 mm, 20 mm and 30 mm respectively as shown in Figure 1. Quartz was the material used to run experiments, and was arranged into 3 monosizes namely 8 mm +5.6 mm, 4 mm +2.8 mm Abstract
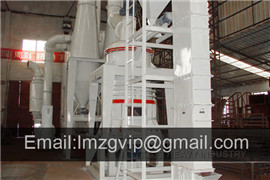
Design and Analysis of Ball Mill For Paint Industries IJSRD
can reducing running cost of ball mill. Optimizing is done by Modeling and Analysis of parts of ball mill by using ‘Finite Element Method’. Keywords:Parameters, ball mill, modeling and analysis I. INTRODUCTION Ball mill is vital equipment used in industries for mineral dressing, ore processing, fertilizers, paint industries, foodThe ball mill Chemical Engineering Beyond Discovery,The balls are usually made of flint or steel and occupy between 30 and 50 per cent of the volume of the mill. The diameter of ball used will vary between 12 mm and 125 mm and the optimum diameter is approximately proportional to the square root of the size of the feed, with the proportionality constant being a function of the nature of the(PDF) Effect of ball size distribution on milling ,the ball mass and between th e ball ma ss an d the mill liners. The si ze reduction depends mainly on the surface are as of the media in interaction (Hukki, 19 54).
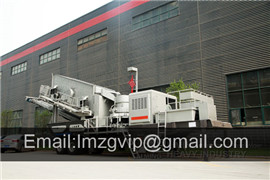
Ball Mill Working Principle And Main Parts GitHub Pages
The main part of the ball mill mainly include feeding part, discharging part, a rotary part, a transmission part (reducer, small gear, motors, electrical control) and other parts. Hollow shaft adopts steel castings, the liner is detachable, slewing gear hobbing with casting, the cylinder body with wearresistant liner, with good resistance to wear.17 Signs of Problems with Ball Mills: Quickly Remove ,High temperature of the ball mill will affact the efficiency. 3 For every 1% increase in moisture, the output of the ball mill will be reduced by 8% 10%. 4 when the moisture is greater than 5%, the ball mill will be unable to perform the grinding operation. 5. The bearing of the ball mill is overheated and the motor is overloaded.Ball Mill RETSCH powerful grinding and homogenization,RETSCH is the world leading manufacturer of laboratory ball mills and offers the perfect product for each application. The High Energy Ball Mill E max and MM 500 were developed for grinding with the highest energy input. The innovative design of both, the mills and the grinding jars, allows for continuous grinding down to the nano range in the shortest

(PDF) Design of Threechamber Ball Mill ResearchGate
3.5 × 13m threechamber ball mill pitch diameter of the mill taken 4 times. 𝑙 4D 14 m ( 2 ) The turning of the ball mill refers to the turning of the barrel of the ball mill when it is workingBall Mill an overview ScienceDirect Topics,Conical Ball Mills differ in mill body construction, which is composed of two cones and a short cylindrical part located between them (Fig. 2.12).Such a ball mill body is expedient because efficiency is appreciably increased. Peripheral velocity along the conical drum scales down in the direction from the cylindrical part to the discharge outlet; the helix Ball mill media optimization Metcom Tech,torque mill test is the mill energy input divided by the solids load. The energy specific cumulative grinding rate at each screen size is calculated from a torquemill test as in the example that follows. Torque mill solids load during test: 11.25 kg (24.8 lb) of ball mill feed sample from plant survey. Sample is reconstituted with water to be
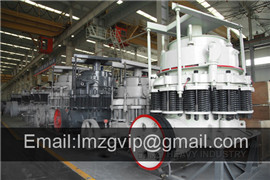
DISINTEGRATION, AGGLOMERATION, AND SIZE
BALL MILLS. Ball mills serve as a final stage of comminution. Balls have a greater ratio of surface area to weight than rods so they are better suited to fine grinding. The length to diameter ratio ranges from less than 1 to about 1.5. Rotation speed is greater than that of rod mills, being 70–80% of critical.Choosing the correct mill screen for your bulk ,Round Hole Cone Mill screen. The round hole screen is widely used for conical milling applications. It is typically used for dry milling, blending, deagglomeration and for reducing the bulk density of spray AMIT 135: Lesson 3 Particle Size Distribution ,There is 5% retained on the 1mm screen. If the total feed was directed to the 0.3mm screen, 40% of the feed would be retained on the screen. 95% of the feed is finer than 1mm and 20% is finer than 0.15mm. The mean size of
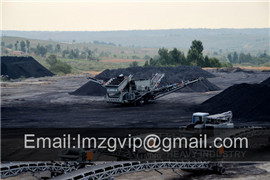
Ball mill characteristics and test conditions Download Table
The experimental mill used was a laboratory size of 209 mm diameter, 175 mm length, providing a total mill volume of 6001 cm3, with a total mass of 5.6 kg of steel balls of 46, 26 and 12.8 mmDesign and Analysis of Ball Mill For Paint Industries IJSRD,can reducing running cost of ball mill. Optimizing is done by Modeling and Analysis of parts of ball mill by using ‘Finite Element Method’. Keywords:Parameters, ball mill, modeling and analysis I. INTRODUCTION Ball mill is vital equipment used in industries for mineral dressing, ore processing, fertilizers, paint industries, foodBond Work Index an overview ScienceDirect Topics,A standard ball mill is 305 mm in internal diameter and 305 mm in internal length charged with 285 balls, as tabulated in Table 2.1. The lowest limit of the total mass of balls is 19.5 Kg. The mill is rotated at 70 rev/min. The process is continued until the net mass of undersize produced by revolution becomes a constant G b.p in the above