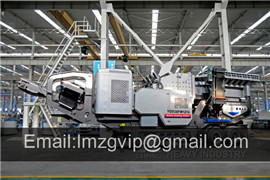
Comminution and classification technologies of iron ore
Iron ore operations commonly employ one or more stages of crushing with screening stages incorporated to remove material meeting product size specifications as soon as possible. Lump product (typically between 6.3 mm and 31.5 mm) attracts a Case Study of Dry HPGR Grinding and ,This publication summarizes some of the features and experiences with dry HPGR processing. A descriptive iron ore case Research of iron ore grinding in a verticalrollermill,Verticalrollermills (VRM) are an energyefficient alternative to conventional grinding technology. One reason is the dry inbed grinding principle. Results

Dry processing of magnetic iron ores addressing cost
AusIMM Iron Ore Conference, Perth, Australia, 2426 July . Paper Number: 86 the cost of grinding to these sizes has been and remains the key 11.24 Metallic Minerals Processing,Wet grinding Neg Neg Dry grinding with air conveying and/or air classification (SCC 30302409)e 28.8 C 26 C Dry grinding without air conveying and/or Iron ore crushing and screening process Fruitfulmill.net,The iron ore processing and production process mainly includes three processes: crushing, grinding and beneficiation. In the crushing process, the threestage
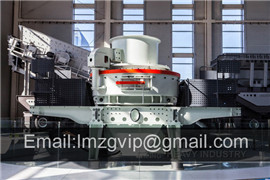
Dry Grinding VS Wet Grinding Mineral
The choice between wet and dry milling is, in general, unimportant in smallscale milling but is a major technical problem when largescale milling in the metallurgical industries is involved. On purely Dry Iron Ore Beneficiation ST Equipment & Technology,Iron ore extraction is mainly performed through open pit mining operations, resulting in significant tailings generation. The iron ore production system usually involves three Fine Dry Grinding of Iron Ore for Pelletizing,Most dry iron ore grinding installations utilizing the standard type rod or ball mill are grinding highgrade natural ores that do not require beneficiation. indirect, watercooled rotary drum, 2) the vertical

(PDF) Development of a Novel Grinding Process to Iron
Highpressure grinding rolls (HPGR) have gained great popularity in the mining industry in the last 25 years or so. One of the first successful applications of the Comminution and classification technologies of iron ore,Iron ore operations commonly employ one or more stages of crushing with screening stages incorporated to remove material meeting product size specifications as soon as possible. Lump product (typically between 6.3 mm and 31.5 mm) attracts a premium price compared to fines product (typically less than 6.3 mm). Dry grinding with HPGR Development of a Novel Grinding Process to Iron Ore,Modern iron ore pelletizing process operations may be divided into two main process sections: feedstock preparation and agglomeration processes. In most plants, the required particle size distribution (PSD) is obtained through the wet ball mill circuit. (2013) Comparative study of the use of HPGR and conventional wet and dry grinding

Pressing iron ore concentrate in a pilotscale HPGR. Part 1
Summary and conclusions. The present work studied the performance of a pilotscale HPGR pressing an iron ore concentrate under a variety of conditions that are consistent with pregrinding. As already observed by Van der Meer and Leite () for iron ore pellet feed pressing and confirmed here, specific throughput tends to drop as thePopulation balance model approach to ball mill ,2 INTRODUCTION Grinding operations are of great importance to the mineral industries and in particular are one of the most important unit operation in the iron ore pelletizing process.VAN DER MEER, F.P.,LEITE, I.L. ENTMME,High Pressure Grinding Rolls (“HPGR”) are applied in all stages of iron ore size reduction, from coarse ore grinding down to pellet feed preparation. In closed circuit operation, fine grinds can be achieved using HPGR in combination with dry or wet classification or a partial product recycle without classification. For fine product cuts,

Mineral Processing Can We Keep It Dry? Kuchling
It would be nice to eventually get to 100% dry processing at all iron ore operations. The link to the article is here “Vale exploring dry stacking/magnetic separation to eradicate tailings dams”. Is dry grinding possible Wet grinding is currently the most common method for particle size reduction and mineral liberation.Iron ore crushing and screening process Fruitfulmill.net,The iron ore processing and production process mainly includes three processes: crushing, grinding and beneficiation. In the crushing process, the threestage closedcircuit crushing is more modern and suitable for highhardness iron ore crushing and can complete the work of ore crushing and partial dissociation, thereby improving the Iron Ore Processing,Crushing,Grinding Plant ,Iron ore is the key raw material for steel production enterprises. Generally, iron ore with a grade of less than 50% needs to be processed before smelting and utilization. After crushing, grinding, magnetic separation,
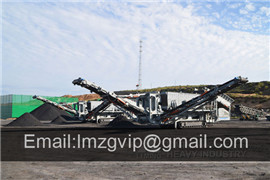
Kpler Dry Bulk Analyst
Kpler is looking for an Analyst to join our global Dry Data Operations Team based in Singapore. The role will involve ensuring a high level of data quality through collection, processing and analysis of Dry Bulk data (Iron Ore/Coal/Ags/Minor Bulks). You will track specific trends occurring in the Dry Bulk market and regularly liaise with both internal and Grindability Studies of Mineral Materials of Different ,of these four materials in dry and wet grinding conditions. It shows that coal and dolomite are easy to grind materials by dry grinding method whereas iron and manganese ores are suitable for wet grinding. It was seen that wet grinding improve the material fineness than dry grinding and maximum 15% improvement in D 80 was seen Development of a Novel Grinding Process to Iron Ore,Modern iron ore pelletizing process operations may be divided into two main process sections: feedstock preparation and agglomeration processes. In most plants, the required particle size distribution (PSD) is obtained through the wet ball mill circuit. (2013) Comparative study of the use of HPGR and conventional wet and dry grinding
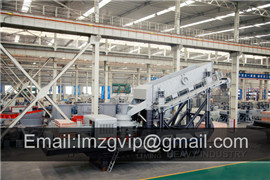
Methods of Ore Pretreatment for Comminution Energy
The grinding aid can be applied in both dry and wet grinding operations. Dry grinding, unlike the wet one, does not require the addition of liquid during the grinding operation. Effect of thermal treatment via furnace on iron ore grinding (100 g, 2.45 GHz, and 1 h) (data source: ). Figure 5. Electromagnetic spectrum. Figure 5Estimation of Grinding Time for Desired Particle Size,A bench test was developed for dry grinding to determine the Bond work index and to know the PSD and hematite liberation in all the three iron ore product samples obtained from the BBM. For each iron ore sample, 700 cc of feed was weighed and added into the BBM. The BBM was set for 100 revolutions in the first iteration.Population balance model approach to ball mill ,2 INTRODUCTION Grinding operations are of great importance to the mineral industries and in particular are one of the most important unit operation in the iron ore pelletizing process.
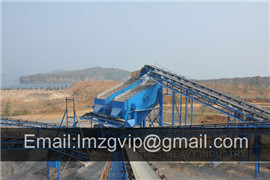
Dry beneficiation of iron ore Mineral Processing
The iron content of the detected reserves averages 46.2 % (1), 49.2 % (2) and 66.1 % (3). An important milestone in dry iron ore beneficiation was achieved by Vale with the Conceição Itabiritos project (Fig. 14) in Minas Gerais, which went into operation in 2014 and beneficiates iron ore with qualities > 40 % Fe.The Effect of Grinding Media on Mineral Breakage ,The mineral composition and content are shown in Table 1.According to the measurement result by MLA, the minerals in the ore were mainly magnetite and quartz, accounting for 32.48% and 61.73%, respectively, and their weight was accounted for 94.21% of the total, indicating that the magnetite ores can be basically considered a two Dry Iron Ore Beneficiation ST Equipment & Technology,Iron ore extraction is mainly performed through open pit mining operations, resulting in significant tailings generation. The iron ore production system usually involves three stages: mining, processing and pelletizing activities. Of these, processing ensures that an adequate iron grade and chemistry is achieved prior to the pelletizing stage.

Kpler Dry Bulk Analyst
Kpler is looking for an Analyst to join our global Dry Data Operations Team based in Singapore. The role will involve ensuring a high level of data quality through collection, processing and analysis of Dry Bulk data (Iron Ore/Coal/Ags/Minor Bulks). You will track specific trends occurring in the Dry Bulk market and regularly liaise with both internal and Process for iron ore pellets production Companhia, Vale ,There are several options available to the grinding operation. It can be performed in or wet or dry, open or closed operations. In the wet grinding process iron ore and water are mixed together and both are added to the mill in adjusted proportions performing a diluted grounded ore pulp.Magnesite Ore Processing: Separation and Calcination,Step 1 Crushing: Crush the raw ore to 100mm with a jaw crusher and a roll crusher. Step 2 Washing: Set a trommel screen to remove the muddy impurities in the ore. Step 3 Grinding: Use a ball mill to grind the raw ore to 95%0.074mm. Step 4 Magnetic separation: Use a magnetic separator to remove iron impurities in the pulp.