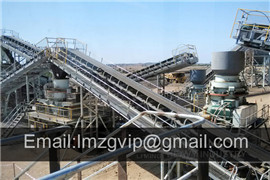
Physical separation of iron ore: magnetic separation
When the iron ore slurry passes through the separating column, the magnetite particles are dragged by the magnetic force to the bottom of the column, while the nonmagnetic particles are carried up to the nonmagnetics chute by the moving water.Developments in the physical separation of iron ore: ,When the iron ore slurry passes through the separating column, the magnetite particles are dragged by the magnetic force to the bottom of the column, and (PDF) Physical separation methods, Part 1: A Review,Magnetic separation is applied in ore process ing for separating magnetic materials, particularly Iron [4]. The advent of magnetic separation found favour in mineral
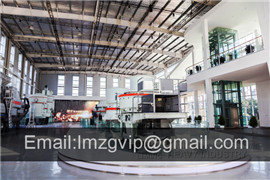
The six main steps of iron ore processing Multotec
Six steps to process iron ore. 1. Screening. We recommend that you begin by screening the iron ore to separate fine particles below the crusher’s CSS before the crushing stage. A Extraction of Iron: Meaning, Purification, & Extraction ,The extraction of iron from its ore is the third and the penultimate process in metallurgy, which is the process of separating metals from their ores. The common Extraction of Iron Metallurgy Blast Furnace ,This concentrated ore is mixed with limestone (CaCO 3) and Coke and fed into the blast furnace from the top. It is in the blast furnace that extraction of iron occurs. The extraction of iron from its ore is a long
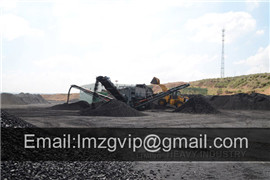
Process and Principle of Magnetic Separation of Iron Ore
Today, I will share with you the magnetic separation process of iron ore. Magnetic Separation Principle Magnetic separation is a beneficiation method that uses Iron ore beneficiation process Prominer (Shanghai) ,Iron ore beneficiation process. 052521; 1,256 Views; icon 0; Others have high magnesium content, and some magnesium is present in magnetite in the Separation process of iron ore,iron ore magnetic ,The beneficiation process of iron ore of different nature is also completely different. First, Strong magnetic iron ore . 1.Single magnetite . Most of the iron minerals

A Process Intensification Approach to Improve
Process Intensification (PI) is a rapidly growing field of research aiming to improve productivity, accelerate the process with higher reaction rates innovatively, improve efficiency, safety, and reduce emissions to fulfill Environmental Social, and Governance (ESG) commitments. The PI approach is also a pathfinding tool to achieve carbon (PDF) ORE SEPARATION BY SCREENING,Sieving is a process of separation of the ore material into multiple grades by particle size [1]. The screen is a vibrating mining machine, that is driven to motion by a rotating of unbalancedFroth flotation process and its application Wiley Online ,Roasting: In this process the sulfide ores are heated to a high temperature in presence of air. Smelting: In this process heat is applied to the ore in order to extract the base metals like silver (Ag), iron (Fe), copper (Cu) etc. Often before roasting, the ore (generally sulfide ores) is partially purified using another important
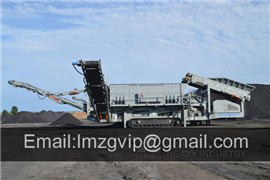
Extraction of Iron Metallurgy Blast Furnace
This concentrated ore is mixed with limestone (CaCO 3) and Coke and fed into the blast furnace from the top. It is in the blast furnace that extraction of iron occurs. The extraction of iron from its ore is a long Extraction of Iron from its ores, Iron dressing, ,S + O 2 → SO 2. 4 P + 5 O 2 → 2 P 2 O 5. Roasting is the process of heating iron ore strongly in dry air for drying the ore and expelling humidity, It is used to increase the percentage of iron in the ore Metals Free FullText Parameter Optimization for ,Hydrogenbased direct reduced iron (HyDRI) produced by fluidized bed has great potential for achieving the target of netzero carbon in steelmaking. However, when magnetite ores were used as feedstock, several process parameters showed influences on its fluidization and reduction behaviors. To confirm the dominant influencing factors and
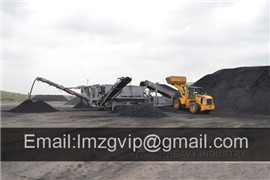
How to Extract Iron from Hematite: Methods and Plants
Coarsegrained hematite refers to iron ore with an embedded particle size of 2mm or more. It is easy to extract iron from this kind of haematite by using gravity separation and magnetic separation. Mediumgrained hematite refers to iron ore with an embedded particle size between 0.02 and 2mm. This type of hematite is also relatively Dephosphorization of nitric acid solutions from the ,We used inorganic salts, acids and bases of analytical grades. Hematite (alpha) was used as an adsorbent for phosphoric acid. The behavior of phosphorus was studied on the two model systems containing iron(III) in the form of oxide or nitrate and phosphoric acid in the presence of nitric acid or lanthanum nitrate denoted by Fe 2 O 3H Magnesite Ore Processing: Separation and Calcination,The processing flow is as follows: Step 1 Crushing: Use a jaw crusher, roll crusher, and vibrating screen to form a twostageclosed circuit crushing system to crush the raw magnesite ore to 1mm. Step 2 Calcination: Send the raw ore into a rotary kiln for calcination at a temperature of 700800°C for 1 hour. Step 3 Crushing: Crush the calcined

Copper, Nickel and IronContaining Cobalt Ore
When using a mixed flotation process to separate coppercobalt ore, butyl xanthate can be used as a collector and BKNL can be used as a regulator for flotation to obtain coppercobalt mixed coarseExtraction of Iron Metallurgy Blast Furnace ,This concentrated ore is mixed with limestone (CaCO 3) and Coke and fed into the blast furnace from the top. It is in the blast furnace that extraction of iron occurs. The extraction of iron from its ore is a long A Process Intensification Approach to Improve ,Process Intensification (PI) is a rapidly growing field of research aiming to improve productivity, accelerate the process with higher reaction rates innovatively, improve efficiency, safety, and reduce emissions to fulfill Environmental Social, and Governance (ESG) commitments. The PI approach is also a pathfinding tool to achieve carbon

Removal of Silica and Alumina as Impurities
Extraction of iron from Sanje ore by single stage magnetic separation or flotation process did not produce high grade iron concentrate with silica and alumina content. This is because Sanje ore has iron mineral particles Iron ore mining and dressing tecscience,In contrast to the direct reduced iron process, the blast furnace process can be operated on a large scale. The blast furnace process accounts for over 80 % of total steel production. In magnetitecontaining rock, there is another possibility of separating gangue and iron ore. As the name magnetite already suggests, this type of iron ore isMetallurgy GitHub Pages,Metallurgy is the set of processes by which metals are extracted from their ores and converted to more useful forms. Metallurgy consists of three general steps: (1) mining the ore, (2) separating and

Dephosphorization of nitric acid solutions from the
We used inorganic salts, acids and bases of analytical grades. Hematite (alpha) was used as an adsorbent for phosphoric acid. The behavior of phosphorus was studied on the two model systems containing iron(III) in the form of oxide or nitrate and phosphoric acid in the presence of nitric acid or lanthanum nitrate denoted by Fe 2 O 3H Steel Raw Materials, Manufacturing Processes, Quality ,Smelting iron, a primitive direct reduction method of separating iron from its ore using a charcoal forge or furnace, probably began in China and India and then spread westward to the area around the Black Sea. The Chalybes, a subject tribe of the Hittites, invented a cementation process about 1400 B.C. to make the iron stronger. The ironMetals Free FullText Parameter Optimization for ,Hydrogenbased direct reduced iron (HyDRI) produced by fluidized bed has great potential for achieving the target of netzero carbon in steelmaking. However, when magnetite ores were used as feedstock, several process parameters showed influences on its fluidization and reduction behaviors. To confirm the dominant influencing factors and

Copper, Nickel and IronContaining Cobalt Ore
When using a mixed flotation process to separate coppercobalt ore, butyl xanthate can be used as a collector and BKNL can be used as a regulator for flotation to obtain coppercobalt mixed coarseMagnesite Ore Processing: Separation and Calcination,The processing flow is as follows: Step 1 Crushing: Use a jaw crusher, roll crusher, and vibrating screen to form a twostageclosed circuit crushing system to crush the raw magnesite ore to 1mm. Step 2 Calcination: Send the raw ore into a rotary kiln for calcination at a temperature of 700800°C for 1 hour. Step 3 Crushing: Crush the calcined,