
THE EFFECT OF BALL MILL OPERATING PARAMETERS ON
operating parameters. Mill speed, mill charge, ball size, and wet grinding are the parameters which have been selected for the present study. It is hoped that the analysis of the data acquired will allow insight as to which parameters will require a functional Influences of operating parameters on dry ball mill ,Fig. 2. Laboratory ball mill and cylpebs used in the tests 2.2.2 The milling conditions The influences of operating parameters such as mill speed (% of Nc), ball filling ratio (J), Optimization of ball mill operating parameters for their ,Optimization of ball mill operating parameters for their effect on mill output and cement fineness by using RSM method January 2014 International Journal of
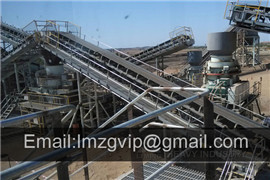
(PDF) Effects of Mill Speed and Air Classifier Speed on
Optimum performance of ball mill could potentially refine Blaine fineness, thereby improving the cement quality. This study investigates the effects of separator Operational parameters affecting the vertical roller mill ,The model shall enable the prediction of the throughput, the particle size distributions around the verticalrollermill circuit, the specific energy consumption and in Ball Mill Parameter Selection & Calculation JXSC,1 Calculation of ball mill capacity. The production capacity of the ball mill is determined by the amount of material required to be ground, and it must have a certain

Variables in Ball Mill Operation Paul O. Abbe®
A Slice Mill is the same diameter as the production mill but shorter in length. Request Price Quote. Click to request a ball mill quote online or call 6303503012 to speak with an Factors Affecting Ball Mill Grinding Efficiency,The following are factors that have been investigated and applied in conventional ball milling in order to maximize grinding efficiency: a) Mill Geometry and Speed Bond (1954) observed grinding efficiency Ball Mill Operation Grinding Circuit Startup & Shutdown ,Disengage ball mill clutch. The mill feed conveyor will automatically stop due to the interlocks between the clutch or cyclone feed pumps and the conveyor. Shut down

parameters affecting the ball mill operating
Contribute to Fruitfulboy/en development by creating an account on GitHub.Influences of operating parameters on dry ball mill ,Fig. 2. Laboratory ball mill and cylpebs used in the tests 2.2.2 The milling conditions The influences of operating parameters such as mill speed (% of Nc), ball filling ratio (J), powder filling ratio (fc), ball size distribution (%), grinding aid dosage (g/Mg) and grinding time (min) were investigated in this study.Energy Use of Fine Grinding in Mineral Processing,The smallest ball size typically charged into ball mills and tower mills is ½ inch (12.5 mm), although media diameters as small as 6 mm have been used industrially in Vertimills. In a laboratory study by Nesset et al .,[ 7 ] a GIS mill charged with 5mm steel shot, and with other operating conditions similarly optimized, achieved high energy

Speeding Up Your Organic Synthesis with Ball
a milling material: agate, 20 min, 800rpm ≙ 13.3 Hz. b 20 min at 20 °C with maximal power input. c 60 in at 80 °C. d 30 min at 80 °C, maximal power input = 300 W.. The effective transfer of energy from the Ball Mills Mineral Processing & Metallurgy,CERAMIC LINED BALL MILL. Ball Mills can be supplied with either ceramic or rubber linings for wet or dry grinding, for continuous or batch type operation, in sizes from 15″ x 21″ to 8′ x 12′. High density Factors that Affect Grinding Efficiency of Your Ball Mill,Firstly, the operation of the operator is undoubtedly another important factor affecting the efficiency of the grinding operation. For example, in the closedcircuit grinding stage, when the sandreturning ratio is too large and exceeds the normal passing capacity of the grinding machine, the phenomenon of running coarse will appear in the
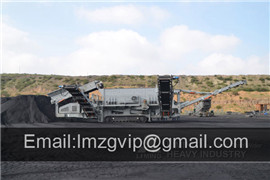
The working principle of ball mill Meetyou Carbide
22 May. The ball mill consists of a metal cylinder and a ball. The working principle is that when the cylinder is rotated, the grinding body (ball) and the object to be polished (material) installed in the cylinder are rotated by the cylinder under the action of friction and centrifugal force. At a certain height, it will automaticallyparameters affecting the ball mill operating , Contribute to Fruitfulboy/en development by creating an account on GitHub.List Factors Affecting Grinding Ball / Media ,WR = R (WS) (CW)/ (DR) (TpH) In addition to wear speed, ball size and recharge practice, charge volume, and feed rate are significant factors affecting the actual production wear rate. Wear speeds are

Factors That Affect Ball Mill Grinder Capacity
As for the dry grinding method, the moisture of raw material can affect ball mill capacity and quality. The higher the moisture content of the milled material will cause saturated or greasy so that the Ball Mill Working Principle And Main Parts GitHub Pages,The main part of the ball mill mainly include feeding part, discharging part, a rotary part, a transmission part (reducer, small gear, motors, electrical control) and other parts. Hollow shaft adopts steel castings, the liner is detachable, slewing gear hobbing with casting, the cylinder body with wearresistant liner, with good resistance to wear.THE EFFECT OF BALL MILL OPERATING PARAMETERS ON ,by mill operating parameters. It is hoped that this work can be used as a precursor to the development of a model that can predict liberation given the various ranges of operating parameters. Mill speed, mill charge, ball size, and wet grinding are the parameters which have been selected for the present study. It is hoped that the analysis

Influences of operating parameters on dry ball mill
Fig. 2. Laboratory ball mill and cylpebs used in the tests 2.2.2 The milling conditions The influences of operating parameters such as mill speed (% of Nc), ball filling ratio (J), powder filling ratio (fc), ball size distribution (%), grinding aid dosage (g/Mg) and grinding time (min) were investigated in this study.Study of the factors increasing the quality and ,drum, rodand ball mill[9], [10], [11]. 4.1. Increasing the density of the grinding media. 4.2. Increasing the contact area between the grinding media components. 4.3. Increasingthe mill's operation in sliding mode by increasing the speed of rotation by 60% of the critical speed. 4.4. Accelerating the passage of the grinding material through theThe Effect of Ball Size Diameter on Milling Performance,An investigation was conducted to determine the effect of the ball diameter sizes on milling operation. A laboratory size ball mill was used with ball media of sizes 10 mm, 20 mm and 30 mm respectively. Quartz was the material used to perform the experiment and was arranged into 3 monosizes namely 8 mm +5.6 mm, 4 mm +2.8

Ball Mill Explained saVRee
For both wet and dry ball mills, the ball mill is charged to approximately 33% with balls (range 3045%). Pulp (crushed ore and water) fills another 15% of the drum’s volume so that the total volume of the drum is 50% charged. Pulp is usually 75% solid (crushed ore) and 25% water; pulp is also known as ‘ slurry ’.Variables in Ball Mill Operation Paul O. Abbe®,A Slice Mill is the same diameter as the production mill but shorter in length. Request Price Quote. Click to request a ball mill quote online or call 6303503012 to speak with an expert at Paul O. Abbe® to help you determine which design and size ball mill would be best for your process. See our Size Reduction Options.The working principle of ball mill Meetyou Carbide,22 May. The ball mill consists of a metal cylinder and a ball. The working principle is that when the cylinder is rotated, the grinding body (ball) and the object to be polished (material) installed in the cylinder are rotated by the cylinder under the action of friction and centrifugal force. At a certain height, it will automatically

Factors Affecting the Efficiency of Ball Mill 439 Words
2, The impact of operating conditions1) Eliminate defects not timely.2) Adjusting undeservedly makes the ball mill running at a short positions. 3, The impact of liner materialThe main parameters affecting the antiwear effect is matching of the two index of hardness and impacting toughness of liner material. If the liner plate has a higherBall Mill Working Principle And Main Parts GitHub Pages,The main part of the ball mill mainly include feeding part, discharging part, a rotary part, a transmission part (reducer, small gear, motors, electrical control) and other parts. Hollow shaft adopts steel castings, the liner is detachable, slewing gear hobbing with casting, the cylinder body with wearresistant liner, with good resistance to wear.Construction and Working of Ball Mill Solution Pharmacy,Construction of Ball Mill. The ball mill consists of a hollow metal cylinder mounted on a shaft and rotating about its horizontal axis. The cylinder can be made of metal, porcelain, or rubber. Inside the cylinder balls or pebbles are placed. The balls occupy between 30 and 50% of the volume of the cylinder. The diameter of the balls depends on