
(PDF) Analysis of the efficiency of the grinding process in
Abstract. Ball mills for fine grinding cement clinker and additives are widely used around the world. To improve the efficiency of a ball grinding the ball mills are transferred in closed circuit(PDF) Grinding in Ball Mills: Modeling and ,The vibratory ball mill (VBM, Sweco, Belgium) consists of a 36 Lcapacity grinding chamber made of an abrasionresistant Determining the Bond Efficiency of industrial grinding ,µm. Note that—in order for no correction factor for ball mill product fineness to apply—the ball mill circuit P80 should be no less than approximately 70 µm

How to Measure Grinding Efficiency
The first two Grinding Efficiency Measurement examples are given to show how to calculate Wio and Wioc for single stage ball Calculation method and its application for energy ,Measurement results of two ball mills in a real ceramic manufacturing plant showed that the proposed calculation models could achieve an accuracy of more than How to Calculate Grinding Mill Operating ,The Bond Equation as found in reference 5 is: W = 10Wi/p0.5 10Wi/p0.5. Where: W = kwh per short ton. Wi = Work Index determined from crushing and grinding tests. P = The size in microns
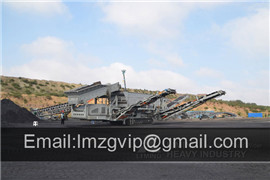
Ball Mill Design/Power Calculation Mineral
Ball Mill Power Calculation Example #1. A wet grinding ball mill in closed circuit is to be fed 100 TPH of a material with a work index of 15 and a size distribution of 80% passing ¼ inch (6350 microns). The Factors Affecting Ball Mill Grinding Efficiency,The following are factors that have been investigated and applied in conventional ball milling in order to maximize grinding efficiency: a) Mill Geometry and Speed Bond (1954) observed grinding efficiency Calculate Ball Mill Grinding Capacity Mineral Processing ,Calculate Ball Mill Grinding Capacity. The sizing of ball mills and ball milling circuits from laboratory grinding tests is largely a question of applying empirical
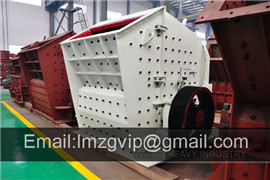
Ball Mill Parameter Selection & Calculation JXSC Machine
1 Calculation of ball mill capacity. The production capacity of the ball mill is determined by the amount of material required to be ground, and it must have a certain Closed circuit ball mill Basics revisited ScienceDirect,1. Introduction. Over the years, ball mill circuits closed with cyclones have become an industry standard, and since the early days, it has been recognised that classification efficiency and circulating load both have a major effect on the efficiency of closed circuit grinding (i.e. its capacity to produce the desired final product).(PDF) Analysis of the efficiency of the grinding process in ,Abstract. Ball mills for fine grinding cement clinker and additives are widely used around the world. To improve the efficiency of a ball grinding the ball mills are transferred in closed circuit
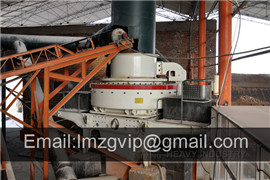
(PDF) Grinding in Ball Mills: Modeling and
The vibratory ball mill (VBM, Sweco, Belgium) consists of a 36 Lcapacity grinding chamber made of an abrasionresistant elastomer, put in vibrating motion by hightensile steel springs [28].Grinding in Ball Mills: Modeling and Process Control,There are three types of grinding media that are commonly used in ball mills: • steel and other metal balls; • metal cylindrical bodies called cylpebs; • ceramic balls with regular or high density. Steel and other metal balls are the most frequently used grinding media with sizes of the balls ranging from 10 to 150 mm in diameter [30].The Effect of Ball Size Diameter on Milling Performance,the other mills, as previously mentioned ball mills have a very low efficiency in terms of utilizing the energy generated towards particle size reduction. The diameter of the balls used in ball mills play a significant role in the improvement and optimization of the efficiency of the mill [4]. The optimum rotation speed of a mill, which is
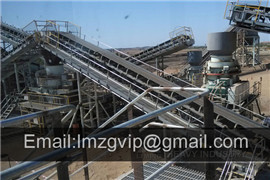
Ball mill media optimization Metcom Tech
mill grinding rate over the material’s grindability as measured in the lab. Mill percent solids optimization has thusly been achieved (McIvor et al., 2000). For media sizing, maximizing the mill grinding rate on a given ore is equivalent to maximizing the mill grinding efficiency. Ores of different grindability will be part of the discussion.GMSG GUIDELINE: DETERMINING THE BOND ,closing screen for the ball mill test one (standard square root of 2 series) mesh size coarser than the plant ball mill circuit P80. If between standard mesh sizes, the finer of the chose two. Results of Bond ball mill tests conducted with closing screens of 75 µm or finer are to be treated with caution. TheInfluences of operating parameters on dry ball mill ,2.2.1 Conventional ball mill A laboratory batch scale conventional ball mill which is made of stainless steel with the internal dimensions of 200 × 200 mm and the volume of 6283 cm3 was utilized in grinding tests. There is no lifter design in the grinding tank. The mill is driven by a 0.37 kW variable speed motor.
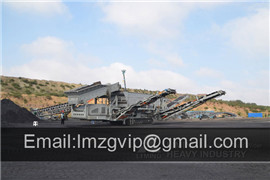
(PDF) ball mill Sheetanshu Pandey Academia.edu
Bond's formula is usually presented in this form: 1 1 E =10×Wi (√ − P 80 √ F 80 ) (1) 1 For the purists, there were two models in existence at the time: the Von Rittinger and Kick models. The ball mill gepinion efficiency is the same as for a SAG mill. For a geardriven ball mill, use the following: Total Ball Mill Motor PowerGrinding efficiency of ball mill calculating equation,One way to calculate a ball mill's grinding efficiency is to divide its total static horsepower (TSH) by its total theoretical tonnage (TPT). This number can then be used to compare different types of mills. A TSH of 1.0 hp/tonne is considered to be very efficient, while a TSH of 2.0 hp/tonne is considered to be moderately efficient.Grinding in Ball Mills: Modeling and Process Control,There are three types of grinding media that are commonly used in ball mills: • steel and other metal balls; • metal cylindrical bodies called cylpebs; • ceramic balls with regular or high density. Steel and other metal balls are the most frequently used grinding media with sizes of the balls ranging from 10 to 150 mm in diameter [30].

Analiza efektywności mielenia w młynach kulowym i
Analysis of process of grinding efficiency in ball and rod mills with various feed parameters D Foszcz1, D Krawczykowski1, T Gawenda1, E KasińskaPilut2 and W Pawlos2 located in Kazakhstan, two highpressure grinding rolls for milling and only one ball mill grinding stage were used. The maximum particle size for roll presses in this plantGrain size and shape fractal characteristics of gangue in ,The model of the ball mill used in this test is SMφ500×500mm test mill,the grinding medium is steel balls, the maximum single charge is 5 Kg, the maximum load of the grinding body is 100 Kg, the power is 1.5 kw, and the speed is 48 rpm. Rolling bearings mainly support the working principle, and the cylinder is driven to rotate through theBall mill media optimization Metcom Tech,mill grinding rate over the material’s grindability as measured in the lab. Mill percent solids optimization has thusly been achieved (McIvor et al., 2000). For media sizing, maximizing the mill grinding rate on a given ore is equivalent to maximizing the mill grinding efficiency. Ores of different grindability will be part of the discussion.

GMSG GUIDELINE: DETERMINING THE BOND
closing screen for the ball mill test one (standard square root of 2 series) mesh size coarser than the plant ball mill circuit P80. If between standard mesh sizes, the finer of the chose two. Results of Bond ball mill tests conducted with closing screens of 75 µm or finer are to be treated with caution. TheThe influence of mill speed and pulp density on the ,the mill. This will result in a coarser grind with a slightly steeper particle size distribution curve (see Graph 4). If one increases the density, the pulp will become too sticky and the ball charge expands. The balls become coated and the grinding efficiency decreases. The pilot mill is also equipped with a sensor measuringBall Mill Calculations PDF Mill (Grinding),Ball Mill Performance & Efficiency S. Description. Symbol. Formula. Example. No. Exp ( ( NB OB ) * 0.49 / 1000 ) NB. OPB. Old production rate, tph. NPB. OB. Old blaine, cm2/gm. Ball Mill Grinding

how to calculate tons per hour ball mill machine
To calculate the tons per hour of a ball mill machine, you will need to know: The diameter of the mill: This is the distance across the widest part of the mill. The length of the mill: This is thehow to calculate false air in ball mill,Mar 08, 2013 · calculation of ball mill grinding efficiency. dear experts . please tell me how to calculate the grinding efficiency of a closed ckt & open ckt ball mill. in literatures it is written that the grinding efficiency of ball mill is very less [less than 10%]. please expalin in a n excel sheet to calcualte the same. thanks. sidhantBall mill grinding media calculation pdf Australian ,calculation for grinding media in ball mill. 20130308· calculation of ball mill grinding efficiency. dear experts . please tell me how to calculate the grinding efficiency of a closed ckt & open ckt ball mill. read more cement mill grinding media calculations china . The mill feed is a calculation of grinding media charging ball mill