
(PDF) REPAIR WELDING OF GEAR SHAFTS OF
Presented in this paper are two methods for repair welding of a total of 8 gear shafts (toothed shafts) of service rollers in the "Topla REPAIR WELDING OF GEAR SHAFTS OF SERVICE ,Abstract: Presented in this paper are two methods for repair welding of a total of 8 gear shafts (toothed shafts) of service rollers in the "Topla valjaonica" rolling mill within Specification for Welding of Industrial and Mill Cranes ,and mill cranes, lifting devices and other material handling equipment. Requirements are also included for modification, weld repair, and postweld treatments of
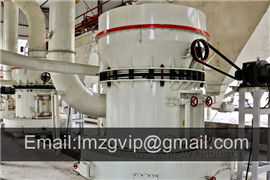
Welding Repair Procedure And Method Statement Pdf
Procedure for welding repair. Welding repairs based on the requirements, location, and service, are classified as the following types: 1. Production weld repair. 2. In Girth Gear Inspection Pre and Post Manufacture,When the gear is mounted on the mill, periodic inspections are required to check alignment of the pinion and gear. This can be done by measuring temperature Cement mill Cracks in the mill ends IMIA,Cement mill Cracks in the mill ends . This case of damage was investigated to decide if repairwelding is a sufficient solution when the ends of a cement

(PDF) Design, fabrication and analysis of
Dedicated welding fixtures are used in the railcar manufacturing industry to fix and stabilise the welded components during the welding assembly process in order to achieve the highest possibleOperations Manual for the McCormick Grist Mill,a wallower, a horizontal face gear and a vertical pinton gear (three photos below). The McCormick Mill utilizes a two step gearing known as “counter gearing.” The Fruitful mill gear repair by welding pdf.md at master,You can not select more than 25 topics Topics must start with a letter or number, can include dashes ('') and can be up to 35 characters long.

Repair Welding an overview ScienceDirect Topics
Problems may arise in the repair welding of machinery and parts due to high carbon content and high impurity levels, and such conditions demand the use of a weld metal that can (PDF) REPAIR WELDING OF GEAR SHAFTS OF ,Presented in this paper are two methods for repair welding of a total of 8 gear shafts (toothed shafts) of service rollers in the "Topla valjaonica" rolling mill within Železara Smederevo. DamageRepair Welding an overview ScienceDirect Topics,Problems may arise in the repair welding of machinery and parts due to high carbon content and high impurity levels, and such conditions demand the use of a weld metal that can accommodate dilution without solidification cracking and has a low hydrogen potential. The compositions frequently used for this purpose are 20Cr–9Ni–3Mo, 23Cr–12Ni (type 309),

(PDF) The repair of foundry defects in steel
Abstract and Figures. Use of welding technology for the repair of steel castings is particularly common in two areas. These include weld surfacing of protrusions that remained incomplete afterWeld repairs Sulzer,Welding widely used repair technology. Welding is a wellestablished technology in the repair of turbine stator and turbine rotor parts. Our carefullydesigned repair procedures offer “good as new” performance of ASSEMBLY PROCESSES Welding FUNDAMENTALS OF ,FUNDAMENTALS OF WELDING 1. Overview of Welding Technology 2. The Weld Joints 3. Physics of Welding 4. Features of a Fusion Welded Joint Used in railroad, repair cracks in ingot and large frame and shaft. ME477 Fall 2004 Kwon 4 19 High Energy beam Welding • Electron Beam Welding
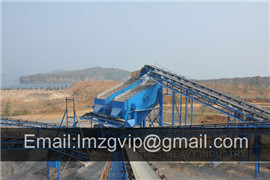
Cement mill Cracks in the mill ends IMIA
Cement mill Cracks in the mill ends . This case of damage was investigated to decide if repairwelding is a sufficient solution when the ends of a cement mill start to crack and are in danger of breaking. To ensure that the damage is repaired reliably, the cause of the damage must be investigated and weld seams examined carefully.How To Weld Repair A Gear Box Casting? Material Welding,Steps to commence the Cast Iron Repair: First of all, drill holes on both sides of the crack to arrest the crack. This will help to eliminate further propagation of the crack into the material. Clean the welding area & surrounding area from any paint, grease, or oil contamination. For welding, I prefer to use the “cold method, or also calledGear Repair PPGWorks,Gear Repair and Rebuilding & Manufacturing all Types of Gears Our unique style of gear repair and rebuilding, reconditioning and recutting on all types of Gears. We can rebuild Gears when they have broken, chips or even worn out teeth, by building the teeth back to size and recutting them or rehobbing them. We will determine the cause of failure and
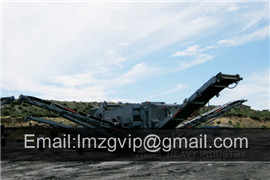
FUNDAMENTALS OF WELDING University of
Although welding has the advantages indicated above, it also has certain limitations and drawbacks (or potential drawbacks): 1 Most welding operations are performed manually and are expensive in terms of labor cost. Many welding operations are considered ‘‘skilled trades,’’ and the labor to perform these operations may be scarce.Gearbox Repair, ReBuilder Co ⚙️HANSON GEAR ,Call (713)7991900 We are a world leader in equipment repair, many years as a premier Gearbox Repair, Rebuilding company.Worm Gear. Free Estimate (713)7991900 info@hansongearworks(PDF) REPAIR WELDING OF GEAR SHAFTS OF ,Presented in this paper are two methods for repair welding of a total of 8 gear shafts (toothed shafts) of service rollers in the "Topla valjaonica" rolling mill within Železara Smederevo. Damage

Repair Welding an overview ScienceDirect Topics
Problems may arise in the repair welding of machinery and parts due to high carbon content and high impurity levels, and such conditions demand the use of a weld metal that can accommodate dilution without solidification cracking and has a low hydrogen potential. The compositions frequently used for this purpose are 20Cr–9Ni–3Mo, 23Cr–12Ni (type 309), (PDF) The repair of foundry defects in steel ,Abstract and Figures. Use of welding technology for the repair of steel castings is particularly common in two areas. These include weld surfacing of protrusions that remained incomplete afterRecommended method for repairing fatigue cracking TWI,Recommended method for repairing fatigue cracking. Where cracking occurs in or adjacent to welded joints, a satisfactory repair may be made by welding. It is important that the cracked material is gouged or machined away sufficiently to permit a full penetration repair weld to be made, with no traces of crack left behind and no new significant

WELDING OF STAINLESS STEELS AND OTHER JOINING
resistance and strength in the weld zone that is an inherent part of the base metal. The purpose.of this booklet is to help designers and manufacturing engineers achieve a better understanding of the welding characteristics of stainless steels, so they may exercise better control over the finished products with respect to welding.Welding Codes and How They're Used American ,Specification for Automotive and Light Truck Weld Quality: Arc Welding. · AWS D14.1. Specification for Welding Earth Moving and Construction Equipment. Applies to all structural welds used in the manufacture of earthmoving and construction equipment. This specification reflects the welding practices employed by manufacturers within theWeld repairs Sulzer,Welding widely used repair technology. Welding is a wellestablished technology in the repair of turbine stator and turbine rotor parts. Our carefullydesigned repair procedures offer “good as new” performance of

GIRTH GEAR Artec Machine
Gear cutting of a split girth gear for a cement mill having an input power of 2200 HP 5. Separate mill A: Damage to mill cylinder, neck or stub endanger girth gear and pinion. Repairs entail extra work for girth gear dismantling. B : Damage to mill cylinder cannot endanger gear teeth. Mill repairs do not entail gear dismantling. KAANU FAC TU How to Repair a Worn Shaft with a Forming ,l grinder fitted with a suitable disk to undercut the shaft by 1/16″ (1.5 mm) around the circumference. Degrease The worn Shaft. Clean the prepared area with Belzona 9111 (Cleaner/Degreaser) to remove all WESERvicEs, WELDINGwps INC LDING NC' Nuclear ,Welding power supply shall be Gold Track II or equivalent. When welding is done remotely, optics for weld puddle shall begin working order. After welding, no nondestructive examination shall be performed for 48 hours. The finished surface of. the repair shall be substantially flush with the surface of the component surrounding the repair..: F