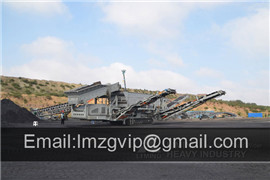
Ball Mill an overview ScienceDirect Topics
Conical Ball Mills differ in mill body construction, which is composed of two cones and a short cylindrical part located between them (Fig. 2.12).Such a ball mill body is expedient because efficiency is appreciably increased. Peripheral velocity along the conical drum Ball Milling an overview ScienceDirect Topics,Ball milling is a way to exfoliate graphite using lateral force, as opposed to the Scotch Tape or sonication that mainly use normal force. Ball mills, like the three roll machine, are a Ball Mill Explained saVRee,For both wet and dry ball mills, the ball mill is charged to approximately 33% with balls (range 3045%). Pulp (crushed ore and water) fills another 15% of the drum’s volume so

Wet Milling vs Dry Milling: The Differences, Advantages
Wet milling, also known as wet grinding, is a process through which particles that are suspended in a liquid slurry are dispersed in that liquid by shearing or Ball Mill Working Principle And Main Parts GitHub Pages,34 行 714 Ball Mill. SKD ball mill is one of the new high efficient grinding What Are the Differences between Dry and Wet ,The water can wash away the fine particles in time to avoid overgrinding. The wet ball mill has a low noise, and low environmental pollution. The wet ball mill has a simple transportation device with less
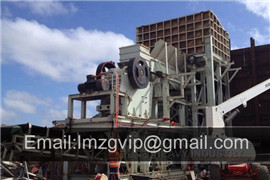
Ball Mill Pharmapproach
A ball mill also known as pebble mill or tumbling mill is a milling machine that consists of a hallow cylinder containing balls; mounted on a metallic frame such that it can be rotated mechanism in wet ball mill machine walkingonwaterfl,The wet type is often equipped with a classifier, and the dry type is configured with a suction and separation device. Both of the dry and wet ball mills are wet ball mill machines mechanism alumnigpe.in,Mechanism In Wet Ball Mill Machine Ball Mill. The Operating Principle Of The Ball Mill. Feb 08 the operating principle of the ball mill consists of following
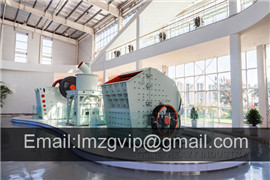
echanism In Wet Ball Mill Machine
Mechanism In Wet Ball Mill Machine cleancutdesignde · Overview Of Milling Techniques For Improving The Jul 01 this technology first developed by liversidge and coworkers is Wet ball milling of niobium by using ethanol, ,This study investigates the effect of using ethanol as the process control agent during the wet ball milling of niobium (Nb). Dried nanocrystal Nb powders, of high purity, with particle sizesBall milling: a green technology for the ,The effect of ball mill on the morphological and structural features of cellulose has been described by Okajima and coworkers. 20 They treated microcrystalline cellulose derived from cotton linters in a planetary ball
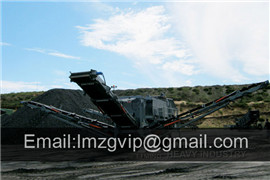
The Effect of Grinding Media on Mineral Breakage
In this paper, the wet ball milling process was used in the laboratory ball milling test. Before grinding, the ball mill was kept idle for 10 minutes and then washed together with the grinding media. Three types of ores were crushed and separated by a jaw crusher, and the ground particle size of 2 mm was selected.Ball Mill Explained saVRee,For both wet and dry ball mills, the ball mill is charged to approximately 33% with balls (range 3045%). Pulp (crushed ore and water) fills another 15% of the drum’s volume so that the total volume of the drum is 50% charged. Pulp is usually 75% solid (crushed ore) and 25% water; pulp is also known as ‘ slurry ’.Metals Free FullText Effect of Ball Milling ,The milling balls with a diameter of 1 mm were also made of Fruitfulium oxide. To avoid the agglomeration and caking of tungsten powder ballmilled by dry milling, the wet milling method was utilized by
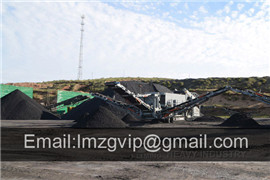
Figure 1. Different mechanisms of comminution:
Ball milling is widely used in industry to mill particulate material. The primary purpose of this process is to attain an appropriate product size with the least possible energy consumption.Grinding in Ball Mills: Modeling and Process Control,55 known as the distribution function [45, 46]) describes the distribution of fragment sizes obtained after a breakage of particles of size xj.Thus, b1j, b2j,,bnj are the mass fractions of particles in size classes 1, 2,,n after a breakage of particles in size class j. The mechanism of breakage is illustrated in [23] by a diagram shown in Fig. 3.Wet Ball Mill for Metal Ores and Nonferrous Metals Wet ,Wet Ball Mill. Feeding size: ≤25mm. Capacity: 0.65615t/h. Motor power: 18.54500kW. Applications: It can deal with metal and nonmetal ores, including gold, silver, copper, phosphate, iron, etc. The ore that needs to be separated and the material that will not affect the quality of the final product when encountering water.
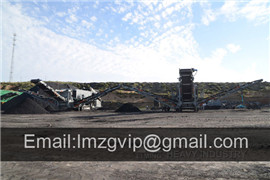
Ball Mill Pharmapproach
A ball mill also known as pebble mill or tumbling mill is a milling machine that consists of a hallow cylinder containing balls; mounted on a metallic frame such that it can be rotated along its longitudinal axis. The balls which could be of different diameter occupy 30 50 % of the mill volume and its size depends on the feed and mill size.Types of Ball Mill Machine Meet Your Industrial Grinding ,As a professional ball mill machine manufacturer and supplier, we can provide types of ball mill according to customer’s requirements. According to production mode: dry ball mill (without adding water) and wet ball mill. According to the process used: dryer mill, superfine ball mill, opencircuit mill, closedcircuit grinding mill, etc.Wet ball milling of niobium by using ethanol, ,This study investigates the effect of using ethanol as the process control agent during the wet ball milling of niobium (Nb). Dried nanocrystal Nb powders, of high purity, with particle sizes
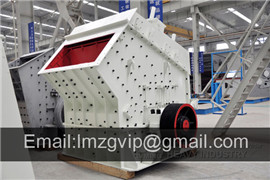
The Effect of Grinding Media on Mineral Breakage
In this paper, the wet ball milling process was used in the laboratory ball milling test. Before grinding, the ball mill was kept idle for 10 minutes and then washed together with the grinding media. Three types of ores were crushed and separated by a jaw crusher, and the ground particle size of 2 mm was selected.(PDF) Grinding in Ball Mills: Modeling and ,The vibratory ball mill (VBM, Sweco, Belgium) consists of a 36 Lcapacity grinding chamber made of an abrasionresistant elastomer, put in vibrating motion by hightensile steel springs [28].Ball Mills Mineral Processing & Metallurgy,CERAMIC LINED BALL MILL. Ball Mills can be supplied with either ceramic or rubber linings for wet or dry grinding, for continuous or batch type operation, in sizes from 15″ x 21″ to 8′ x 12′. High density

How it Works: Crushers, Grinding Mills and
The feed enters one end of the ball mill, and discharges out the other end. Ball mills vary greatly in size, from large industrial ball mills measuring more than 25 ft. in diameter to small mills used for sample Grinding in Ball Mills: Modeling and Process Control,55 known as the distribution function [45, 46]) describes the distribution of fragment sizes obtained after a breakage of particles of size xj.Thus, b1j, b2j,,bnj are the mass fractions of particles in size classes 1, 2,,n after a breakage of particles in size class j. The mechanism of breakage is illustrated in [23] by a diagram shown in Fig. 3.Wet Ball Mill for Metal Ores and Nonferrous Metals Wet ,Wet Ball Mill. Feeding size: ≤25mm. Capacity: 0.65615t/h. Motor power: 18.54500kW. Applications: It can deal with metal and nonmetal ores, including gold, silver, copper, phosphate, iron, etc. The ore that needs to be separated and the material that will not affect the quality of the final product when encountering water.
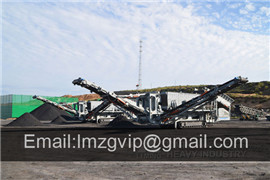
Ball Mills Laboratory Grinding Mill Latest Price,
Find here Ball Mills, Laboratory Grinding Mill manufacturers, suppliers & exporters in India. 10 Mild Steel Ball Mill / Wet Ball Mill /Continous ball mill, Capacity: 250kg1500kg, 500 ₹ 1.26 Lakh Get Latest Price . Ms Metals Free FullText Effect of Ball Milling ,The milling balls with a diameter of 1 mm were also made of Fruitfulium oxide. To avoid the agglomeration and caking of tungsten powder ballmilled by dry milling, the wet milling method was utilized by Morphology Study of Particle Breakage Mechanisms in a ,Highspeed stirred mills are utilized to grind particles below 10mm. Grinding sulphide minerals to as low as 10mm achieve adequate mineral liberation for successful downstream mineral processing operations, such as flotation and leaching. Particle breakage mechanism such as fracture or abrasion, determines the morphological surface features of the