
Mechanism of magnetite iron ore concentrate
The grinding method and its associated parameters strongly affect the physical properties of the iron ore concentrate. Ball milling (BM) and Highpressure grinding rolls (HPGR) are commonly employed for grinding iron ore concentrate,. In BM, the The six main steps of iron ore processing Multotec,3. Feeding the crusher (Reclaim) The surge pile allows a constant supply of material to be fed into the mill, which ensures consistent results and stability in the ore recovery Iron Ore Pelletizing Process: An Overview,The iron ore production has significantly expanded in recent years, owing to increasing steel demands in developing countries.
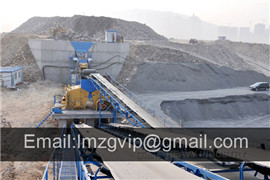
Iron processing Definition, History, Steps, Uses,
iron processing, use of a smelting process to turn the ore into a form from which products can be fashioned. Included in this article also is a discussion of the mining of iron and of its preparation for smelting. Iron (Fe) is a (PDF) Iron Ore Pelletizing Process: An Overview,A process report on the effect of grind, temperature, and pellet size upon in the ironmaking process. Iron ore pellets were made Iron Ore Processing,Crushing,Grinding Plant ,1. Magnetite ore stage grindingmagnetic separation process The stage grindingmagnetic separation process mainly utilizes the characteristics of magnetite that can be enriched under coarse grinding conditions, and at

(PDF) Iron ore pelletization ResearchGate
The iron ore pelletizing process has been studied by using a statistical mathematical model to predict and optimize the sintering conditions of magnesteltic pellets with MnO2 additions. TheHow to Extract Iron from Hematite: Methods and Plants,After three grindings, the concentrate grade of original ore was less than 57%, and the recovery rate was less than 10%. After the magnetic roastingweak Iron Ore Processing an overview ScienceDirect Topics,In the process developed by Das and coworkers (2000), the tailings are mixed with clay and a fluxing material (4050 % tailing, 3050 5 clay and 1015 % fluxing material). The raw

Iron ore beneficiation process Prominer (Shanghai)
The beneficiation process refers to the production process in which the mined ore undergoes various operations to obtain a concentrate that meets the smelting Comminution and classification technologies of iron ore,The Sino Iron project started its first full year of commercial operation in produced and exported approximately 17 million wet metric tons of iron ore concentrate (Citic Annual Report). In , Sino Iron shipped more than 19 million wet metric tons to CITIC’s special steel plants and other Chinese and Asian steel mills (Citic Mechanism of magnetite iron ore concentrate ,The grinding method and its associated parameters strongly affect the physical properties of the iron ore concentrate. Ball milling (BM) and Highpressure grinding rolls (HPGR) are commonly employed for grinding iron ore concentrate,. In BM, the particle size was decreased by impact and attrition breakage, whereas size reduction in
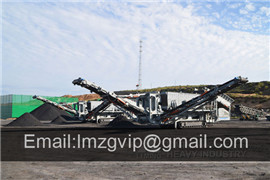
Development of a Novel Grinding Process to Iron Ore
The earliest industrial application of high pressure grinding rolls (HPGR) at comminution was in 1984 in the cement industry. Since then, the equipment has been widely applied in mining activities. Despite the rapid spread across the industry, several challenges are still present in the equipment’s application, especially considering the complex ore Development of Ironmaking Technology by the Direct ,nology (FIT), and the other is a movingbed process for continuous ironmaking with gaseous reduction of iron ore concentrate (MBIT). These technologies are designed to produce iron directly from iron concentrate without requiring pelletization/sintering and cokemaking. They take advantage of the high reactivity of theInvestigation of Liberation Properties and Mineral Fracture ,The liberation degree of silver minerals in the grinding products was as high as 77.33% after using SCSM to grind the ore to 85% passing 74 μm, suggesting that most silver minerals in the ore

11.23 Taconite Ore Processing US EPA
The average iron content of pellets is 63 percent. 11.23.2 Process Description25,41 Processing of taconite consists of crushing and grinding the ore to liberate ironbearing particles, concentrating the ore by separating the particles from the waste material (gangue), and pelletizing the iron ore concentrate.Four kinds of iron ore processing and production process,The iron ore processing and production process refers to the production process in which the mined iron ore must be processed and produced by various operations to obtain concentrates that meet the smelting requirements. Mainly include: ore crusher crushing and vibrating screen screening, ball mill grinding and classifier classification; How to Extract Iron from Hematite: Methods and Plants,After three grindings, the concentrate grade of original ore was less than 57%, and the recovery rate was less than 10%. After the magnetic roastingweak magnetic separation process, the concentrate grade of hematite reached 62%, and the recovery rate reached 80%, which fundamentally solved the problem of both beneficiation and recovery.
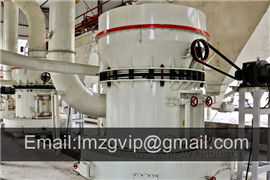
PROCESSES OF BENEFICIATION AND EXTRACTION OF
Considering the continuous decrease of titanium, rutile and ilmenite mineral deposits, There are costeffective ways to produce titanium using vanadium titanomagnetite as a raw material, becomes more and more important. In this study, vanadium titanomagnetite concentrate was obtained Magnetic separation for downstream production at the Tebin Iron ore crushing and screening process Fruitfulmill.net,The iron ore processing and production process mainly includes three processes: crushing, grinding and beneficiation. In the crushing process, the threestage closedcircuit crushing is more modern and suitable for highhardness iron ore crushing and can complete the work of ore crushing and partial dissociation, thereby improving the Iron Concentrate Particles MDPI,Iron ore concentrate is an output product from processed iron ores that have been milled (crush, grind, magnetic separation, flotation) to separate deleterious elements and produce a highquality product. Sintering and pelletizing are economic and widely used agglomeration processes to prepare iron ore fines/iron concentrate for

Iron Ore Concentrate Particle Size Controlling Through
Nowadays, the HPGR (highpressure grinding rolls) is an intermediate step between filtering and balling in the most modern iron ore pelletizing operation. The operation debottlenecks filtering process and reduces pressure over the typical milling process to control particle size to the balling. The present study evaluated aspects of microwave Pressing iron ore concentrate in a pilotscale HPGR. Part 2: ,Abstract. The roller press, also called highpressure grinding rolls (HPGRs), has been successfully used for over 25 years in increasing the surface area of iron ore concentrates for pellet feed production prior to green pellet formation. In spite of the long track record of application, there have been no systematic mathematical modelingMinerals Free FullText Recovering Iron from ,Iron ore tailings (IOTs) are a form of solid waste produced during the beneficiation process of iron ore concentrate. In this paper, iron recovery from IOTs was studied at different points during a process

Development of a Novel Grinding Process to Iron Ore
The earliest industrial application of high pressure grinding rolls (HPGR) at comminution was in 1984 in the cement industry. Since then, the equipment has been widely applied in mining activities. Despite the rapid spread across the industry, several challenges are still present in the equipment’s application, especially considering the complex ore Development of Ironmaking Technology by the Direct ,nology (FIT), and the other is a movingbed process for continuous ironmaking with gaseous reduction of iron ore concentrate (MBIT). These technologies are designed to produce iron directly from iron concentrate without requiring pelletization/sintering and cokemaking. They take advantage of the high reactivity of theExisting and New Processes for Beneficiation of Indian Iron ,BHJ ore, which is known to be a difficulttotreat iron ore, can be upgraded to a concentrate having 66% Fe at an iron recovery of 72% using reduction roastingmagnetic separation . There are some other reports of successful application of reduction roasting process for lowgrade Indian iron ores [ 20 ].
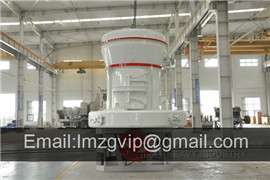
11.23 Taconite Ore Processing US EPA
The average iron content of pellets is 63 percent. 11.23.2 Process Description25,41 Processing of taconite consists of crushing and grinding the ore to liberate ironbearing particles, concentrating the ore by separating the particles from the waste material (gangue), and pelletizing the iron ore concentrate.PROCESSES OF BENEFICIATION AND EXTRACTION OF ,Considering the continuous decrease of titanium, rutile and ilmenite mineral deposits, There are costeffective ways to produce titanium using vanadium titanomagnetite as a raw material, becomes more and more important. In this study, vanadium titanomagnetite concentrate was obtained Magnetic separation for downstream production at the Tebin Beneficiation of Iron Ore Mineral Processing,The Iron Ore Process Flowsheet. In place of initially grinding 85 to 90% minus 325, the grind if coarsened to 8085% minus 325mesh will result in greater initial tonnage treated per mill section. are