
Ball Mill Explained saVRee
For both wet and dry ball mills, the ball mill is charged to approximately 33% with balls (range 3045%). Pulp (crushed ore and water) fills another 15% of the drum’s volume so 行星式球磨仪PM100德国RETSCH(莱驰)研磨仪粉碎仪,Download. The Planetary Ball Mill PM 100 is a powerful benchtop model with a single grinding station and an easytouse counterweight which compensates masses up to 8 The working principle of ball mill Meetyou Carbide,22 May. The ball mill consists of a metal cylinder and a ball. The working principle is that when the cylinder is rotated, the grinding body (ball) and the

Ball Mill Working Principle And Main Parts GitHub Pages
34 行 714 Ball Mill Working Principle. To be chosen according to the Ball Mill Pharmapproach Unifying for progress,A ball mill also known as pebble mill or tumbling mill is a milling machine that consists of a hallow cylinder containing balls; mounted on a metallic frame such that it can be rotated Factors Affecting Ball Mill Grinding Efficiency,The following are factors that have been investigated and applied in conventional ball milling in order to maximize grinding efficiency: a) Mill Geometry and Speed Bond (1954) observed grinding efficiency
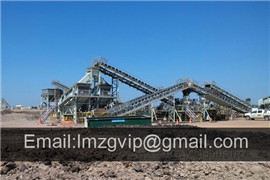
constituents of a ball mill
Ball mill internal structure and composition The ball mill is the key equipment for crushing the material after it has been broken. It is widely used in cement, constituents of a ball mill,FullerTraylor Ball Mills are the most robust design in the industry. ; Performance optimization of an industrial ball mill for chromite . Keywords: coarse grinding circuit, ball Constituents of a ball mill,1028T13:10:14+00:00 High energy ball milling process for nanomaterial synthesis. It is a ball milling process where a powder mixture placed in the ball mill is subjected to

Ball Mill an overview ScienceDirect Topics
Conical Ball Mills differ in mill body construction, which is composed of two cones and a short cylindrical part located between them (Fig. 2.12).Such a ball mill body is expedient because efficiency is appreciably increased. Peripheral velocity along the conical drum scales down in the direction from the cylindrical part to the discharge outlet; the helix Module7 unit3 NSNT Module 7 Ballmilling,The fine blending of the constituents of powder reduces the diffusion distance to few microns. The dominating processes at this stage are fracturing and cold welding. metals, etc. Ball mill can be used to grind ores and other materials which can be both wet and dry. On the basis of removal of end products, ball mill can be of two types: Performance optimization of an industrial ball ,The energy consumption in the ball mill was found to be 6.5 kWh/t of ore with a targeted product size below 1 mm. The BWI of the ores varied from 5.8 to 7.8 kWh/t to reduce the particle size below 100 μ m, but in real

Ball milling improves extractability and antioxidant
Inonotus obliquus has been used as a folk remedy for a long time. An improved method using fine grinding by ball mill was investigated, and the main chemical components and physicochemical properties of Inonotus obliquus powders were analysed. The Inonotus obliquus fine grinding powders were prepared by pulverising the coarse Ball Mill Working Principle And Main Parts GitHub Pages,Ball Mill Working Principle. To be chosen according to the grinding material, material is composed of a ball mill feed end of the hollow shaft is arranged in the tube body, when the ball mill cylinder rotation time, grinding body due to inertia and centrifugal force, the effects of friction, making it attached to the cylinder liner on the Ball Mill Parameter Selection & Calculation JXSC,1 Calculation of ball mill capacity. The production capacity of the ball mill is determined by the amount of material required to be ground, and it must have a certain margin when designing and selecting. There are many factors affecting the production capacity of the ball mill, in addition to the nature of the material (grain size, hardness,

Factors Affecting Ball Mill Grinding Efficiency
The following are factors that have been investigated and applied in conventional ball milling in order to maximize grinding efficiency: a) Mill Geometry and Speed Bond (1954) observed grinding efficiency Ball Mill GardenBallistics,Ball mills are machines which are used to reduce the granular size of powdered compounds and chemicals; its use is also a highly efficient method to mix/blend multiple substances together. This is an important requirement for good pyrotechnic compounds, the finer the grain of a pyrotechnic compound and how well it has been constituents of a ball mill,Ball mill internal structure and composition The ball mill is the key equipment for crushing the material after it has been broken. It is widely used in cement, silicate products, new building materials, refractories, fertilizers, black and nonferrous metal beneficiation and glass ceramics, and other industries, the dry or wet grinding of a variety

constituents of a ball mill
Ball Mill: Operating principles, components, Uses . 11/1/ · A ball mill also known as pebble mill or tumbling mill is a milling machine that consists of a hallow cylinder containing balls; mounted on a metallic frame such that it can be rotated along its longitudinal axis The balls which could be of different diameter occupy 30 50 % of the mill volume and its Comparative Study on Improving the Ball Mill Process ,The ball mill process parameters discussed in this study are ball to powder weight ratio, ball mill working capacity and ball mill speed. As Taguchi array, also known as orthogonal array design, adds a new dimension to conventional experimental design, therefore, Orthogonal array (L9) was carefully chosen for experimental design to Ball Mill RETSCH powerful grinding and homogenization,RETSCH is the world leading manufacturer of laboratory ball mills and offers the perfect product for each application. The High Energy Ball Mill E max and MM 500 were developed for grinding with the highest energy input. The innovative design of both, the mills and the grinding jars, allows for continuous grinding down to the nano range in the shortest

(PDF) Design of Threechamber Ball Mill ResearchGate
In this paper, the design method of three chamber ball mill is introduced. Comchambered with the design of Φ 3.5 × 13m threechamber ball mill, the design process of ball mill is described inSpeeding Up Your Organic Synthesis with Ball ,a milling material: agate, 20 min, 800rpm ≙ 13.3 Hz. b 20 min at 20 °C with maximal power input. c 60 in at 80 °C. d 30 min at 80 °C, maximal power input = 300 W.. The effective transfer of energy from the Performance optimization of an industrial ball ,The energy consumption in the ball mill was found to be 6.5 kWh/t of ore with a targeted product size below 1 mm. The BWI of the ores varied from 5.8 to 7.8 kWh/t to reduce the particle size below 100 μ m, but in real

What is Ball Milling Process? ball mills supplier
This article takes dry ball milling as an example to introduce the ball milling process. First, select the appropriate size and weight of the grinding medium according to the particle size of the grinding material. The material is loaded into the cylinder by the hollow shaft at the feed end of the ball mill machine.Ball Mill Parameter Selection & Calculation JXSC,1 Calculation of ball mill capacity. The production capacity of the ball mill is determined by the amount of material required to be ground, and it must have a certain margin when designing and selecting. There are many factors affecting the production capacity of the ball mill, in addition to the nature of the material (grain size, hardness, Cement Ball Mill JXSC Machine,The cement ball mill is mainly used for grinding the finished products and raw materials of cement plants, and is also suitable for grinding various ore and other grindable materials in industrial and
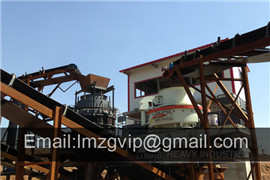
constituents of a ball mill
Ball mill internal structure and composition The ball mill is the key equipment for crushing the material after it has been broken. It is widely used in cement, silicate products, new building materials, refractories, fertilizers, black and nonferrous metal beneficiation and glass ceramics, and other industries, the dry or wet grinding of a variety constituents of a ball mill,The main components of the ball mill Bestcrushers's blog. The main components of the ball mill Earlier in the overall structure of the several types of mill The following will introduce the basic structure of the main components of the mill 221 Rotary Rotary parts include: cylinder,energysaving grinding plant grinding head (end cap and hollow shaft), linings, ,