
Modeling and estimation of cutting forces in ball helical
Ventura et al. [ 4] described an approach for modeling the cutting forces in the helical milling process based on the analysis of tool contact angle and depth of cut. The model could be used to predict the behavior and magnitude of the force acting on the Modeling and Analysis of HighEnergy Ball Milling ,3.1 Effects of Ball Milling Velocity and Ball Volume Fraction. EDEM as a powerful software enables to collect data from the dynamic behavior of the entire ball Ball milling: a green mechanochemical approach ,Ball milling is a process, in which the moving balls apply their kinetic energy to the milled material, break chemical bonding and produce fresh surfaces by fracturing material particles. Xray photoelectron spectroscopy
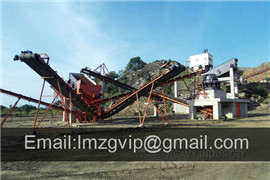
Ball Milling an overview ScienceDirect Topics
Ball milling technique, using mechanical alloying and mechanical milling approaches were proposed to the word wide in the 8th decade of the last century for preparing a wide Mechanistic Modeling of the Ball End Milling Process for ,A mechanistic modeling approach to predicting cutting forces is developed for multiaxis ball end milling of freeform surfaces. The workpiece surface is represented (PDF) Modelling of the HighEnergy Ball Milling Process,Similar results were reached by Zhang et al. [65] for ball−milled activated carbon, in which the specific surface area and pore volume diminished from 2137 m 2 ·g

(PDF) Grinding in Ball Mills: Modeling and
The process control in a ball mill grinding circuit faces severe difficulties due to the following well known characteristics: • the process is nonlinear with immeas urable disturbances and行星式球磨仪PM100德国RETSCH(莱驰)研磨仪粉碎仪,Download. The Planetary Ball Mill PM 100 is a powerful benchtop model with a single grinding station and an easytouse counterweight which compensates masses up to 8 Ball Milling method for synthesis of nanomaterials,This process of ball milling is done approximately 100 to 150 hrs to get uniform fine powder. 4. Ball milling is a mechanical process and thus all the structural

What is Ball Milling Process Dry Ball Milling Process
The ball milling process is generally divided into two types, the dry ball milling process, and the wet ball milling process. This article takes dry ball milling as an example to introduce Modeling and Analysis of HighEnergy Ball Milling ,3.1 Effects of Ball Milling Velocity and Ball Volume Fraction. EDEM as a powerful software enables to collect data from the dynamic behavior of the entire ball milling simulation process. In order to explore the milling efficiency of the models, the average speed of balls, the maximum speed of balls, and the magnitude of torque on the milling Ball Milled SiW Alloys: Part I. Microstructural and Phase ,In this first part of a twopart study of the synthesis, microstructure and electrochemical properties of ball milled silicontungsten alloys (Si 100x W x, x = 15, 20, 25, 30), the ball milling process is discussed in detail.The phase evolution was quantitatively followed during milling, allowing for a detailed understanding of the ball milling process.

General Cutting Dynamics Model for FiveAxis BallEnd
Abstract. Fiveaxis ballend milling is used extensively to machine parts with sculptured surfaces. This paper presents the general cutting dynamics model of the ballend milling process for machine tools with different fiveaxis configurations. The structural dynamics of both the tool and workpiece are considered for the prediction of chatter (PDF) Modelling of the HighEnergy Ball Milling Process,Abstract and Figures. In this paper, the milling parameters of high energy ball mill (Fritsch Pulverisette 7) like vial geometry, number and size of balls and speed of the mill were modelled andGeometric modeling of the rubbing zone limits in 3axis ,Fontaine M, Moufki A, Devillez A, Dudzinski D (2007) Modelling of cutting forces in ballend milling with tool–surface inclination: Part I: predictive force model and experimental validation. J Mater Process Technol 189(1–3):73–84.
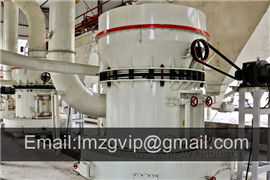
The prediction of cutting forces in the ballend milling
DOI: 10.1016/08906955(94)900523 Corpus ID: 111097279; The prediction of cutting forces in the ballend milling process—I. Model formulation and model building procedure @article{Feng1994ThePO, title={The prediction of cutting forces in the ballend milling process—I. Model formulation and model building procedure}, author={HsiYung Fabrication of Aloe vera nanopowder by high energy ball ,Faraji et al. [17] briefed that in high energy ball milling; high power collisions from the balls were subjected to a dust mixture, positioned in a ball mill. The rotation orders of the bowl and the balls were contrary; the centrifugal forces were consecutively coordinated. Yang et al. [13] claimed that coarsegrained structures Grinding in Ball Mills: Modeling and Process Control,the milling process takes place during rotation as a result of the transfer of kinetic energy of the moving grinding media into the grinding product. The design of a ball mill can vary significantly depending on the size, the equipment used to load the starting material (feeders), and the system for discharging the output product.

Modelling of the HighEnergy Ball Milling Process
In this paper, the milling parameters of high energy ball mill (Fritsch Pulverisette 7) like vial geometry, number and size of balls and speed of the mill were modelled and discussed. Simulations through discrete element method (DEM) provide correlation between the milling parameters. A mathematical model is used to improve and develop this process.Ball Milling method for synthesis of nanomaterials,This process of ball milling is done approximately 100 to 150 hrs to get uniform fine powder. 4. Ball milling is a mechanical process and thus all the structural and chemical changes are produced by mechanical energy. I have seen an interesting image at for ball milling method at wikipedia. You can see the image here. Advantages of ball Ball Milled SiW Alloys: Part I. Microstructural and Phase ,In this first part of a twopart study of the synthesis, microstructure and electrochemical properties of ball milled silicontungsten alloys (Si 100x W x, x = 15, 20, 25, 30), the ball milling process is discussed in detail.The phase evolution was quantitatively followed during milling, allowing for a detailed understanding of the ball milling process.
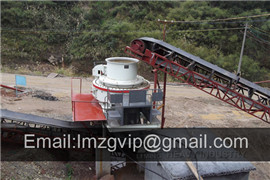
General Cutting Dynamics Model for FiveAxis BallEnd
Abstract. Fiveaxis ballend milling is used extensively to machine parts with sculptured surfaces. This paper presents the general cutting dynamics model of the ballend milling process for machine tools with different fiveaxis configurations. The structural dynamics of both the tool and workpiece are considered for the prediction of chatter Study on Preparation and Characterization of ,Taking advantage of the stateoftheart graphene preparation technologies in China and abroad, this work studied the preparation processes of graphene for road applications based on the preliminary highspeed BallMillingEnabled Reactivity of Manganese Metal,The process has been optimised and its mechanism explored by CV measurements, radical trapping, and EPR spectroscopy. Control experiments identify the action of ball milling rather than mortar and pestle is necessary to realise the effective activation of manganese, which can then be used in either solution or a ball mill for

Geometric modeling of the rubbing zone limits in 3axis
Fontaine M, Moufki A, Devillez A, Dudzinski D (2007) Modelling of cutting forces in ballend milling with tool–surface inclination: Part I: predictive force model and experimental validation. J Mater Process Technol 189(1–3):73–84.ball milling process: Topics by Science.gov OSTI.GOV,The optimum parameters for the milling process were ball speed of 350 r/min, solid/liquid ratio of 1:10, raw material particle size with 0.5 mm, and number of balls of 20 (steel ball, Φ = 10 mm), grinding for 30 min. In comparison with water milling process, alkaline milling treatment could increase the enzymaticModelling of the HighEnergy Ball Milling Process,In this paper, the milling parameters of high energy ball mill (Fritsch Pulverisette 7) like vial geometry, number and size of balls and speed of the mill were modelled and discussed. Simulations through discrete element method (DEM) provide correlation between the milling parameters. A mathematical model is used to improve and develop this process.

Fabrication of Aloe vera nanopowder by high energy ball
Faraji et al. [17] briefed that in high energy ball milling; high power collisions from the balls were subjected to a dust mixture, positioned in a ball mill. The rotation orders of the bowl and the balls were contrary; the centrifugal forces were consecutively coordinated. Yang et al. [13] claimed that coarsegrained structures Ball Milling method for synthesis of nanomaterials,This process of ball milling is done approximately 100 to 150 hrs to get uniform fine powder. 4. Ball milling is a mechanical process and thus all the structural and chemical changes are produced by mechanical energy. I have seen an interesting image at for ball milling method at wikipedia. You can see the image here. Advantages of ball What is Ball Milling Process Dry Ball Milling Process ,The ball milling process is generally divided into two types, the dry ball milling process, and the wet ball milling process. This article takes dry ball milling as an example to introduce the ball milling process. First, select the appropriate size and weight of the grinding medium according to the particle size of the grinding material.