
Process engineering with planetary ball mills
Processes inside planetary ball mills are complex and strongly depend on the processed material and synthesis and, thus, the optimum milling Grind Molycop,SIZE Molycop manufactures forged grinding balls for use in ball milling and regrind applications in nominal sizes from 1.0” to 4.0” in Specific alloy Study of Grinding Ball Quality Properties During ,In particular, the specific consumption of grinding balls is lower by 20–30% compared with cylindrical pebbles due a significantly lower probability of

Impact of planetary ball mills on corn stover characteristics
The grinding balls used in this study have different properties. Alumina balls have a low specific gravity of 4.09 g/cm 3 and steel balls are 1.9 times heavier than Study of Grinding Ball Quality Properties During ,The governing effect of macrostructure quality on impact resistance is established by experiment for grinding balls 50 and 60 mm in diameter prepared by screw rolling. It is Grinding Balls and Other Grinding Media: Key consumables,Tower Mills: 0.5”1.5” grinding balls are recommended. The normal top size of media used is 1025mm, but even smaller grinding balls can be used for very fine
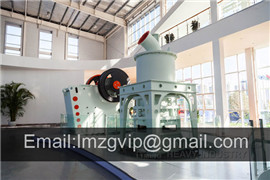
Forged Steel Grinding Balls Alpha Grinding Media
Surface hardness of our forged steel grinding balls ranges between 5862 HRC with volumetric hardness ranging between 5562 HRC. Our steel balls for use in Influence of properties of grinding bowls in the ,Working with the highest rotational speeds is ideal: 1. The grinding balls will distribute better on the entire grinding bowl surface and result in a best possible grinding effect. If the rotational speeds are too low the grinding Grinding Ball Design Metallurgist & Mineral ,Critical ball design features include new size and mass, worn size distribution, chemistry, hardness, microstructure, toughness, internal stress, and stability of microstructure. These factors determine

Buy Cast Iron Grinding Balls, Properties of Cast Iron Ball
The Cast iron grinding ball is excellent in surface quality, toughness, and resistance to impact and abrasion. It won't crack and lose circularity quickly. Grinding media is used in Process engineering with planetary ball mills,Processes inside planetary ball mills are complex and strongly depend on the processed material and synthesis and, thus, the optimum milling conditions have to be assessed for each individual system. The present Study of Grinding Ball Quality Properties During ,In particular, the specific consumption of grinding balls is lower by 20–30% compared with cylindrical pebbles due a significantly lower probability of breakage during operation for the reason of a lack of stress boundaries (corners). An improvement the milling quality of ground material and an increase in mill productivity is noted.

The Properties and Performance of Cast Iron Grinding Media
Cast iron balls have been used for decades as a grinding media in all types of grinding applications. Early applications of cast iron grinding balls in mineral processing operations were disastrous due to spalling and premature breakage. Better control and understanding of a high chromium cast iron metallurgical system have led to the use of Ball milling as an important pretreatment technique in ,The chemical resistance of the grinding balls is also an important property to consider for mechanochemical pretreatment. Different construction materials are available such as stainless steel, hardened steel, tungsten carbide, agate, Fruitfulium oxide, and silicon nitride [47, 48]. Different grinding balls have different surface roughness andGrinding Media Growth Steel,In ball milling applications, the diameter of the balls, mill and throw action of the charge provides a lowimpact environment– hence maximum abrasion resistance of steel balls is the desired characteristic
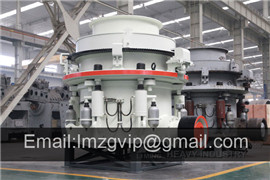
Consumption of steel grinding media in mills A review
Klimpel, 1982, Klimpel, 1983 has drawn attention to the importance of rheological properties in ball mill grinding on the specific rates of breakages of minerals in the presence and absence of chemical additives. Meloy and Crabtree (1967) have studied the effect of viscosity and surface tension of various liquids on grinding efficiencyGrinding Balls and Other Grinding Media: Key consumables,Tower Mills: 0.5”1.5” grinding balls are recommended. The normal top size of media used is 1025mm, but even smaller grinding balls can be used for very fine grinding. Isa Mills: <0.1” grinding balls are recommended. The Isa Mill is more efficient when using small media (i.e. highchrome steel balls).Grinding Media Union Process,Backed by our longstanding commitment to customer satisfaction, we ensure quality manufacturing and reliable supply of grinding balls and media specifically engineered to meet the requirements of your most

Grinding Media 911Metallurgist
Effect of Ball Size and Properties on Mill Grinding Capacity Current ball milling theory suggests that grinding capacity is influenced by the size of balls charged to the mill. In selecting the appropriate ball (PDF) Failure of Steel Grinding Balls ResearchGate,Show abstract. A survey of nondestructive techniques used for inspection of bearing steel balls. Article. Mar . MEASUREMENT. Hua Yu Zhang. Chuanwei Zhang. Chenglong Wang. Fengqin Xie.Mechanical properties and corrosion resistance of ,This research aims to determine mechanical properties of grinding ball FexMn10Al 1.25C alloys. The grinding ball alloys were prepared by an induction furnace under argon atmosphere. Al and C levels, 10% and 1.25% respectively, in FeAlMn grinding ball were kept constant while Mn content was varied by 15%, 20% and 25%.

The Properties and Performance of Cast Iron Grinding Media
Cast iron balls have been used for decades as a grinding media in all types of grinding applications. Early applications of cast iron grinding balls in mineral processing operations were disastrous due to spalling and premature breakage. Better control and understanding of a high chromium cast iron metallurgical system have led to the use of Grinding Media Growth Steel,In ball milling applications, the diameter of the balls, mill and throw action of the charge provides a lowimpact environment– hence maximum abrasion resistance of steel balls is the desired characteristic Stainless steel grinding balls for mining / ball mill,AISI steel grinding balls for ball mill applications typically have a tolerance of ±0.05/±0.10 and a density of 7.70 to 7.95. Exceptions include Al series 1XXX and Al 6061 which have the same tolerance but a density of 2.71

Grinding Media Union Process
Backed by our longstanding commitment to customer satisfaction, we ensure quality manufacturing and reliable supply of grinding balls and media specifically engineered to meet the requirements of your most (PDF) Study On The Performance Of High ,The highest ball wear rates were observed for fine granite grinding under dry (120 mg/cycle) and wet (129 mg/cycle) conditions. The lowest wear rate (ca. 50 mg/cycle) was observed for coarseInfluence of properties of grinding bowls in the ,Working with the highest rotational speeds is ideal: 1. The grinding balls will distribute better on the entire grinding bowl surface and result in a best possible grinding effect. If the rotational speeds are too low the grinding
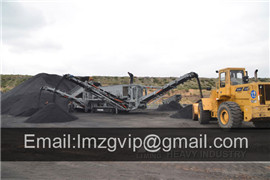
Grinding Media Stanford Materials
The high wearresistant YSZ grinding media effectively eliminate product contamination and lengthen the service life of the grinder. These special features make YSZ grinding media especially suitable for sensitive products and critical applications. YSZ grinding media are widely used for high viscosity, wet grinding, and dispersion. PropertiesGrinding Balls For Mining info@grindingballsforsale,February 24, agico News. Grinding Balls For Mining is an indispensable Grinding Media for ball mills. As the main grinding medium, steel balls play a vital role in the process index and final grinding fineness. Knowing and understanding steel balls is convenient for purchasing in batches with high quality and low price, and serving The Development of Material Grinding Ball in Ballmill ,ball grinding and. liners to determine their chemical . composition by means of Spectrometer testing. After spectrometer testing was conducted it is known that the material used in the imported grinding balls and liners contain carbon (C) above 2.1%, it can be concluded that the material belongs to the category of White cast Iron. The second