
(PDF) Grinding in Ball Mills: Modeling and
The vibratory ball mill (VBM, Sweco, Belgium) consists of a 36 Lcapacity grinding chamber made of an abrasionresistant (PDF) INVESTIGATION OF EFFECTS OF GRINDING MEDIA ,Ball mills are equipments which has balls as grinding media and used for last step of grinding process. There are many factors which effect grinding performance Ball mill media optimization Metcom Tech,plant ball mill’s grinding efficiency (Fig. 1). The functional performance parameters “mill grinding rate through the size of interest,” and “cumulative mill grinding
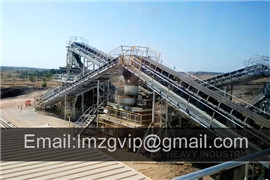
grinding media recharge inside ball mill formula.md at
Contribute to dinglei/en development by creating an account on GitHub.Grinding Media ME Elecmetal,InMill Tracking: Simulation of grinding media size distribution inside the mill, as a function of ball size, discharge size (grate slot), daily charges and theoretical wear (ME Grinding Grinding Media Charge Motion inside Mill,where D is the mill diameter in feet and Nc is the critical speed of the mill in r.p.m. The above formula is based on the assumption that there is no slip between the ball charge and mill shell and, to allow a

Ball Mill Grinding Theory Crushing
Open Circuit Grinding. The object of this test was to determine the crushing efficiency of the ballmill when operating in open circuit. The conditions were as follows: Feed rate, variable from 3 to 18 grinding media recharge inside ball mill formula,Figure 86 The total volume inside the mill is given by Vm 4 D2 mL 1 2 Lc L L 1 Dt/Dm 3 1 Dt/Dm 816 The density of the charge must account for all of the material in the mill Grinding Media Recharge Inside Ball Mill Formula,A population balance model of ball wear in grinding mills. Nov 01, For this particular mill, we suggest a ball recharge of 0.005 balls hour for the balls with
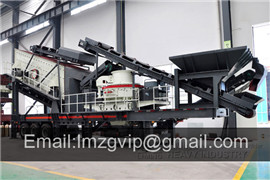
grinding media recharge inside ball mill formula
TECHNICAL NOTES 8 GRINDING R. P. King · Figure 8.6. The total volume inside the mill is given by Vm 4 D2 mL 1 2(Lc L) L 1 (Dt/Dm) 3 1 Dt/Dm (8.16) The density of the The Effect of Grinding Media on Mineral Breakage ,The breakage and liberation of minerals are the key to fluidized mining for minerals. In the ball milling process, steel balls function as not only a grinding action implementer but also energy carrier to determine the breakage behavior of ores and the production capacity of the mill. When ground products present a much coarse or much Quantifying the energy efficiency of fine grinding circuits,In the first survey the ball mill was underperforming due to the low density in the mill, which was rectified in the second survey. The ball mill was grinding to a P 80 of 50 to 70 µm, therefore the traditional marker size (75 µm) was not applicable, and this can be seen by the increase in SSE for coarser sizes as the marker size approached P
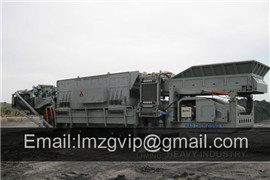
Calculation method and its application for energy
For QMP10T ball mill, the grinding media and raw materials are gradually mixed in the fi rst six seconds after the ball mill is started, which consumes an averageGrinding Medium an overview ScienceDirect Topics,The ball mill is a tumbling mill that uses steel balls as the grinding media. The length of the cylindrical shell is usually 1–1.5 times the shell diameter ( Figure 8.11 ). The feed can be dry, with less than 3% moisture to minimize ball coating, or Ball Mill an overview ScienceDirect Topics,Mechanical Crushing and Grinding. Oleg D. Neikov, in Handbook of NonFerrous Metal Powders (Second Edition), Tumbling Ball Mills. Tumbling ball mills or ball mills are most widely used in both wet and dry systems, in batch and continuous operations, and on small and large scales.. Grinding elements in ball mills travel at different velocities.
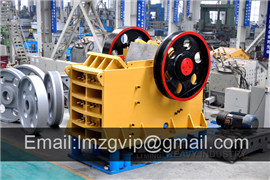
Study of steel ball recharge and consumption in a wet
Request PDF Study of steel ball recharge and consumption in a wet cement industrial mill via a population balance model A population balance model is applied to a steel ball mill. ExperimentalBall Mills Mineral Processing & Metallurgy,CERAMIC LINED BALL MILL. Ball Mills can be supplied with either ceramic or rubber linings for wet or dry grinding, for continuous or batch type operation, in sizes from 15″ x 21″ to 8′ x 12′. High density Grinding Media Union Process,Backed by our longstanding commitment to customer satisfaction, we ensure quality manufacturing and reliable supply of grinding balls and media specifically engineered to meet the requirements of your most
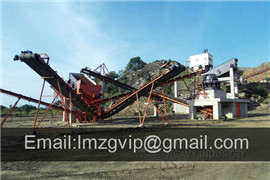
grinding media recharge inside ball mill formula
Figure 86 The total volume inside the mill is given by Vm 4 D2 mL 1 2 Lc L L 1 Dt/Dm 3 1 Dt/Dm 816 The density of the charge must account for all of the material in the mill including the media which may be steel balls in a ball mill or large lumps of ore in an autogenous mill or a mixture in a semiautogenous mill.grinding media recharge inside ball mill formula,TECHNICAL NOTES 8 GRINDING R. P. King · Figure 8.6. The total volume inside the mill is given by Vm 4 D2 mL 1 2(Lc L) L 1 (Dt/Dm) 3 1 Dt/Dm (8.16) The density of the charge must account for all of the material in the mill including the media which may be steel balls in a ball mill, or large lumps of ore in an autogenous mill or a mixture in a semi Advances in Mechanical Engineering , Vol. 13(3) 1–9 ,In general, the industrial ball mills rotational speed operates at 70%~80% of critical speed.22 To understand the interrelation between mill speed and heat transfer, the effect of mill speed on charge temperature for ball filling of J=25% is investigated, as shown in Figure 2. The larger particles represent the grinding media and the smaller
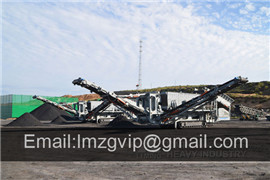
Consumption of steel grinding media in mills A review
According to Moema et al. (2009), in some instances, media wear can constitute up to 40–45% of the total cost of comminution. An estimated consumption of steel grinding media of around 600,000 tons p.a. in the 1980s already gives an indication of the scale of the problem ( Malghan, 1982).Grinding Medium an overview ScienceDirect Topics,The ball mill is a tumbling mill that uses steel balls as the grinding media. The length of the cylindrical shell is usually 1–1.5 times the shell diameter ( Figure 8.11 ). The feed can be dry, with less than 3% moisture to minimize ball coating, or MODULE #5: FUNCTIONAL PERFOMANCE OF BALL ,• Ball mill specific grinding rate • Ball mill grinding efficiency The circuit output is defined as the production rate of fines by the circuit. It is calculated from three values: 1. The dry ore feed rate to the circuit (t/h). 2. The % fines in the circuit feed. 3. The % fines in the circuit product. Use this equation to solve for circuit

(Received: February 1, ; Accepted: November 4, )
J o u r n a l o f Journal of Mining and Metallurgy, 52 A (1) () 1 10 #Corresponding author: alex.jankovic@Fruitful A COMPARISON OF WEAR RATES OF BALL MILL GRINDING MEDIA A. Jankovic#, T. Wills, S. Dikmen Fruitful Process Technology and Innovation, Brisbane, AustraliaBall Mill Parameter Selection & Calculation JXSC,1 Calculation of ball mill capacity. The production capacity of the ball mill is determined by the amount of material required to be ground, and it must have a certain margin when designing and selecting. There are many factors affecting the production capacity of the ball mill, in addition to the nature of the material (grain size, hardness, Grinding Balls and Other Grinding Media: Key consumables,Tower Mills: 0.5”1.5” grinding balls are recommended. The normal top size of media used is 1025mm, but even smaller grinding balls can be used for very fine grinding. Isa Mills: <0.1” grinding balls are recommended. The Isa Mill is more efficient when using small media (i.e. highchrome steel balls).

grinding media recharge inside ball mill formula
Figure 86 The total volume inside the mill is given by Vm 4 D2 mL 1 2 Lc L L 1 Dt/Dm 3 1 Dt/Dm 816 The density of the charge must account for all of the material in the mill including the media which may be steel balls in a ball mill or large lumps of ore in an autogenous mill or a mixture in a semiautogenous mill.Grinding Media Recharge Inside Ball Mill Formula,A population balance model of ball wear in grinding mills. Nov 01, For this particular mill, we suggest a ball recharge of 0.005 balls hour for the balls with diameters of 30.7 mm and 26.9 mm, while for balls with diameter of 40.5 mm, we suggest a ball recharge of 0.01 balls hour.grinding media recharge inside ball mill formula,The ball mill is a tumbling mill that uses steel balls as the grinding media. The length of the cylindrical shell is usually 1–1.5 times the shell diameter (Figure 8.11).The feed can be dry, with less than 3% moisture to minimize ball coating, or slurry containing 20–40% water by weight. Read More EFFECTS OF GRINDING MEDIA SHAPES ON BALL MILL