
Ball Mill Design/Power Calculation Mineral
The basic parameters used in ball mill design (power calculations), rod mill or any tumbling mill sizing are; material to be Calculate and Select Ball Mill Ball Size for ,Based on his work, this formula can be derived for ball diameter sizing and selection: Dm <= 6 (log dk) * d^0.5 where D m = the Grinding Mill Computer Model AusIMM,sizing and tonnage. 3.5 Pebble Mill Design This reverts to the Morgärdshammar method and is similar to the AM calculation 3.6 Tower Mill The tower

Ball Mill Parameter Selection & Calculation JXSC Machine
The quality and surface area of forged steel balls of various sizes are shown in Table 112. A kind of Because of the wear of steel balls in the mill production Ball Mill Design/Power Calculation LinkedIn,The basic parameters used in ball mill design (power calculations), rod mill or any tumbling mill sizing are; material to be ground, characteristics, Bond Work How to Calculate and Solve for Critical Mill of Speed Ball ,The image above represents critical mill of speed. To compute for critical mill of speed, two essential parameters are needed and these parameters are Mill

How can one select ball size in ball milling and
More balls with small size results in fine powder. As a thumb rule powder to be milled should be taken as 25% of total ball weight. If the quantity of charge is very less then milling balls willball mill calculations, grinding media filling degree, ball ,online live calculators for grinding calculations, Ball mill, tube mill, critical speed, Degree of filling balls, Arm of gravity, mill net and gross power(PDF) DESIGN AND FABRICATION OF MINI BALL ,26600 Pekan, Pahang, Malaysia, Phone: +6094246255; Fax: +6094246222. *. Email: [email protected]. ABSTRACT. This project is to design and fabricate the mini ball mill that can grind the solid
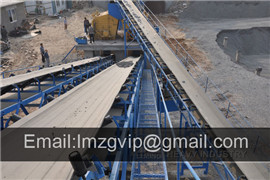
How to Calculate and Solve for Water Activity Ball Mill
Now, Click on Ball Mill Sizing under Materials and Metallurgical Now, Click on Water Activity under Ball Mill Sizing. The screenshot below displays the page or Ball mill media optimization Metcom Tech,A previous literature review on ball mill media sizing (McIvor, 1997) was updated (Staples et al., 1997; Banasi et al., 1999; Orford et al, 2006; LaMarsh, ). The main findings are mill speed are used to calculate the energy input. The specific energy input (E, in kWh/t) is the energy input divided by the mill solids load. TheGrinding Mill Computer Model AusIMM,sizing and tonnage. 3.5 Pebble Mill Design This reverts to the Morgärdshammar method and is similar to the AM calculation 3.6 Tower Mill The tower mill calculation is based on the ball mill design sheet, but is simplified in that the mill design section is omitted. A simple tower mill factor of 70% allows the mill power to be estimated.
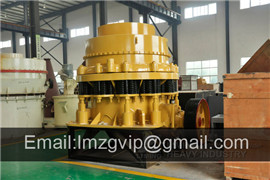
MODELING THE SPECIFIC GRINDING ENERGY AND BALL
21 CONCLUSIONS Continued In the present work, equations were also derived, giving: zthe ballmill power drawP as a function of its dimensions: internal mill diameter D and length L, zthe ballmill power drawP as a function of the feed D f (mm) and the product size d (mm), the Bond work index w i (kWh/short ton) and the mill throughput Ball Mill an overview ScienceDirect Topics,Conical Ball Mills differ in mill body construction, which is composed of two cones and a short cylindrical part located between them (Fig. 2.12).Such a ball mill body is expedient because efficiency is appreciably increased. Peripheral velocity along the conical drum scales down in the direction from the cylindrical part to the discharge outlet; the helix Fruitful code for ball mill sizing calculation · ,Contribute to changjiangsx/Fruitful development by creating an account on GitHub.
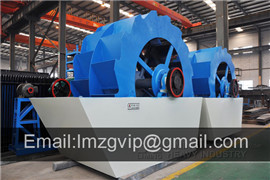
github
ball mill sizing calculation. THE OPTIMAL BALL DIAMETER IN A MILL Strona główna. The optimal ball diameter in a mill 333 The grinding efficiency of the narrow particle size frac3 easy steps to calculate ball mill capacity bulkonline,Step 2. Ball mill drum dimensions. Specify the length and capacity of the drum. If not available, specify the length and diameter of the drum. Step 3 (the final). Grinding bodies. Specify the weight of grinding bodies. You can simply specify a fill ratio for the drum if you do not know the exact weight of grinding bodies. Done!Ball Mill Working Principle And Main Parts GitHub Pages,Ball Mill Working Principle. To be chosen according to the grinding material, material is composed of a ball mill feed end of the hollow shaft is arranged in the tube body, when the ball mill cylinder rotation time, grinding body due to inertia and centrifugal force, the effects of friction, making it attached to the cylinder liner on the
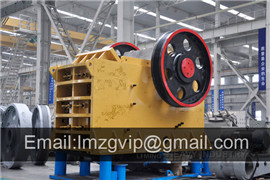
Method to Determine the Ball Filling, in Miduk Copper
to ball filling variation in the mill. The results obtained from this work show, the ball filling percentage variation is between 1.2– 3.7% which is lower than mill ball filling percentage, according to the designed conditions (15%). In addition, acquired load samplings result for mill ball filling was 1.3%.Energy Use of Fine Grinding in Mineral Processing,Fine grinding, to P80 sizes as low as 7 μm, is becoming increasingly important as mines treat ores with smaller liberation sizes. This grinding is typically done using stirred mills such as the Isamill or Stirred Media Detritor. While fine grinding consumes less energy than primary grinding, it can still account for a substantial part of a mill’s Ball Mill Application and Design Paul O. Abbe,Ball Mill Application and Design. Ball mills are used the size reducing or milling of hard materials such as minerals, glass, advanced ceramics, metal oxides, solar cell and semiconductor materials, nutraceuticals and pharmaceuticals materials down to 1 micron or less. The residence time in ball mills is long enough that all particles get
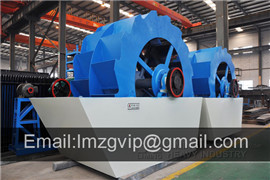
Energy Use of Fine Grinding in Mineral Processing
Fine grinding, to P80 sizes as low as 7 μm, is becoming increasingly important as mines treat ores with smaller liberation sizes. This grinding is typically done using stirred mills such as the Isamill or Stirred Media Detritor. While fine grinding consumes less energy than primary grinding, it can still account for a substantial part of a mill’s CALCULATION OF THE REQUIRED SEMIAUTOGENOUS ,primary wet autogenous mill (WAM) and a series of ball mills. WAM is customary chosen either based on examination of analogous equipment specifications, or from the evidence of very expensive commercial and semicommercial testing that requires large sampling, much time and high investment [1]. The current practice of exploratory (PDF) ball mill Sheetanshu Pandey Academia.edu,The detailed calculation methods for determination of mill dimensions to yield a particular power draw (at a mill shell) is beyond the scope of this Memorandum. Ebm = Etotal ESAG = 8.04 4.50 = 3.54 kWh/tonne ( 13 ) Determine the SAG and ball mill motor sizes required for 2000 tonnes/hour. Using Equations 9 and 10: Total SAG Motor Power
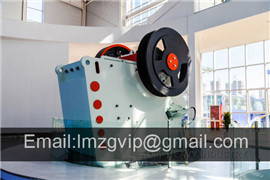
TECHNICAL NOTES 8 GRINDING R. P. King Mineral Tech
The geometry of a mill with conical ends is shown in Figure 8.6. The total volume inside the mill is given by Vm 4 D2 mL 1 2(Lc L) L 1 (Dt/Dm) 3 1 Dt/Dm (8.16) The density of the charge must account for all of the material in the mill including the media which may be steel balls in a ball mill, or large lumps of ore in angithub,ball mill sizing calculation. THE OPTIMAL BALL DIAMETER IN A MILL Strona główna. The optimal ball diameter in a mill 333 The grinding efficiency of the narrow particle size frac3 easy steps to calculate ball mill capacity bulkonline,Step 2. Ball mill drum dimensions. Specify the length and capacity of the drum. If not available, specify the length and diameter of the drum. Step 3 (the final). Grinding bodies. Specify the weight of grinding bodies. You can simply specify a fill ratio for the drum if you do not know the exact weight of grinding bodies. Done!

Ceramic Ball Mill Lining Bricks & Grinding Media
The high impact of conventional ball mills is not needed in vibro mils. Instead a large number of low energy impacts are necessary using small grinding media with high vibration or rotation rate. Recommended grinding media : Recommended media charge : 60 70% of mill’s useful vol. Calculation of media load. Example :Method to Determine the Ball Filling, in Miduk Copper ,to ball filling variation in the mill. The results obtained from this work show, the ball filling percentage variation is between 1.2– 3.7% which is lower than mill ball filling percentage, according to the designed conditions (15%). In addition, acquired load samplings result for mill ball filling was 1.3%.Bond formula for the grinding balls size calculation,The calculation formula is below: B the grinding balls diameter, mm; A the correction factor (for grinding balls A = 20,17; for cilpence A = 18,15); F the feedstock grain size in 80% of the material, μm; K the grinding correction coefficient (for wet grinding 350; for dry grinding 355); S the grind material bulk