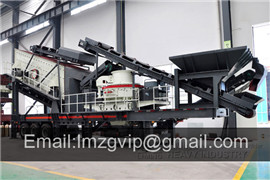
Mineral processing metallurgy Britannica
mineral processing, art of treating crude ores and mineral products in order to separate the valuable minerals from the waste rock, or gangue. It is the first process that most ores What is Grinding? Definition from Corrosionpedia,Grinding is an abrasive machining process that uses a grinding wheel or grinder as the cutting tool. Grinding is a subset of cutting, as grinding is a true metal COMMINUTION: Liberation, Crushing, Grinding LinkedIn,Comminution in the mineral processing plant takes place in a sequence of crushing and grinding (and/or milling). Crushing reduces particle size of runofmine ore
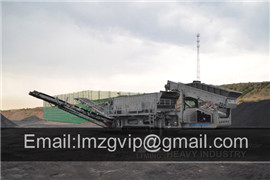
Grinding materials processing Britannica
cutlery. In cutlery: Cutlery manufacture. and tempering it correctly; (3) grinding the blade to a cutting edge and removing all traces of forging and heat treatment; (4) polishing the Grinding Process Mineral Processing,Grinding Process. In the previous chapter, the various “laws” of comminution which have been propounded have been studied in relation to the physical process of size reduction and to the available Grinding Equipment Mineral Processing,Determining an optimal grinding size can maximize the recovery of target minerals in the subsequent flotation process. The grinding size is too large, and some ore particles and

Do You Understand The Grinding And Classifying Process
The preparatory work before mineral dressing generally includes crushing and screening, grinding classification, hand sorting and washing, among which grinding Crushing Mineral Processing,In mineral processing, the reduction of minerals by crushing and grinding may be regarded as having one or other of two main objectives: the attainment of a size what is grinding in mineral Mining & Quarry Plant,grinding mills mineral processing equipment software. Minerals Processing Plant,Mineral Processing Plant Equipments Mineral Processing Equipment. what is
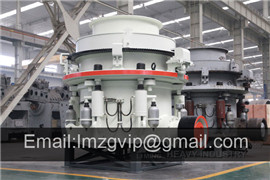
Mineral Processing Design and Operations ScienceDirect
In the second type, known as high pressure grinding roll (HPGR), the mineral sizes are reduced by compressive and interparticle pressure. The forces responsible for communication in each case are illustrated and the mathematical laws involved are explained, using solved examples. Mineral Processing Design and Operations: An (PDF) Overview of Mineral Processing Methods,The objective of this lesson is to provide the details of size reduction methods involved in mineral processing using grinding methods and equipment. View fulltext. Technical Report.Comminution Britannica,In mineral processing: Comminution. In order to separate the valuable components of an ore from the waste rock, the minerals must be liberated from their interlocked state physically by comminution. As a rule, comminution begins by crushing the ore to below a certain size and finishes by grinding Read More; nanoparticles

Grinding Equipment Mineral Processing
Determining an optimal grinding size can maximize the recovery of target minerals in the subsequent flotation process. The grinding size is too large, and some ore particles and nonore particles cannot be separated, thus preventing their flotation. If the particle size is too fine, the bubbles that rise during the flotation will push the veryCrushing and Grinding Process JXSC Machine,The ore size reduction process involves two steps: crushing and grinding. The grinding process is the final operation of making the mineral to dissociate from the monomer and making the particle size Automation Appilications in Mineral Processing Plants,Automation of mineral processing is developing fast, which brings more benefits to the plants. Come to Mining Pedia and see applications of automation! +86 13810565920; and is used in the grinding circuit of the beneficiation plant to detect the grading particle size. The instrument is equipped with a computer, an output instrument
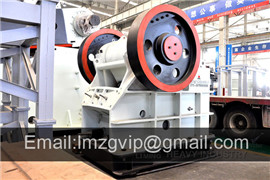
The core benefits for precision grinding PES Media
Thanks to its upgradeable modular system, the machine can be adapted to match individual requirements, while the use of highspeedmachining (HSM) delivers efficient, highprecision form grinding. Available with a choice of distances between centres of 400/650/1,000/1,600mm, the S31 has a centre height of 175mm and a grinding wheel Application of stirring mill in grinding of nonmetallic ,Before grinding, the dispersant sodium hexametaphosphate was added, and the corundum ball in the grinding was stirred( Φ= 1.2 mm) and small ball( Φ= When the volume ratio of 0.8mm) is 0.8:1.5, the medium filling rate is 70%, the grinding mass fraction is 70%, the stripping speed is 800r/min, and the grinding time is 180min, the grinding: be in mineral processing Dice,Plausible(grinding, be in mineral processing) ⋁ Evidence: 0.61. ¬ Typical(grinding, be in mineral processing) Imprint
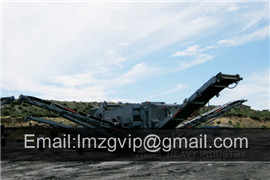
what is grinding in mineral Mining & Quarry Plant
grinding mills mineral processing equipment software. Minerals Processing Plant,Mineral Processing Plant Equipments Mineral Processing Equipment. what is the meaning of mineral stone grinding. Information on active gem, mineral, and jewellery making clubs in Western Washington, USA. SKD is one of the modernized grinding mill Machine A process mineralogy approach to study the efficiency of ,In Eq. (), dE is the specific energy for grinding (kwh/t), k is the grinding constant, and dx/x n is the variations of particle size during grinding.The main missing factor in most comminutionMineral Processing SpringerLink,Crushing and grinding is the most costly step in mineral processing because the power needed to liberate the minerals is very high. In this sense, grinding is commonly said to be the key to good mineral treatment and the major consumer of energy, accounting for up to 50% of a concentrator’s energy consumption ( Table 6.3 ).
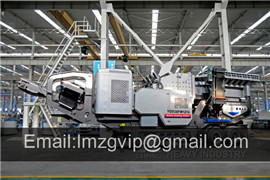
Comminution Britannica
In mineral processing: Comminution. In order to separate the valuable components of an ore from the waste rock, the minerals must be liberated from their interlocked state physically by comminution. As a rule, comminution begins by crushing the ore to below a certain size and finishes by grinding Read More; nanoparticlesMINERAL PROCESSING MILLING Internet Archive,MINERAL PROCESSING MILLING Introduction Milling, sometimes also known as fine grinding, pulverising or comminution, is the process of reducing materials to a powder of fine or very fine size. It is distinct from crushing or granulation, which involves size reduction to a rock, pebble or grain size. Milling is used to produce a varietyDo You Understand The Grinding And Classifying Process ,The preparatory work before mineral dressing generally includes crushing and screening, grinding classification, hand sorting and washing, among which grinding classification is the followup technology of crushing and screening and also an important process in the predressing stage. By grinding the ore to a certain degree of fineness,

Grinding Equipment Mineral Processing
Determining an optimal grinding size can maximize the recovery of target minerals in the subsequent flotation process. The grinding size is too large, and some ore particles and nonore particles cannot be separated, thus preventing their flotation. If the particle size is too fine, the bubbles that rise during the flotation will push the verySome Questions about Grinding Stage Before Mineral ,3.One closedstage grinding process with control classification, which is very uneven feed size, difficult to properly load balls, and low grinding efficiency, is rarely used in mineral processingAutomation Appilications in Mineral Processing Plants,Automation of mineral processing is developing fast, which brings more benefits to the plants. Come to Mining Pedia and see applications of automation! +86 13810565920; and is used in the grinding circuit of the beneficiation plant to detect the grading particle size. The instrument is equipped with a computer, an output instrument

Application of stirring mill in grinding of nonmetallic
Before grinding, the dispersant sodium hexametaphosphate was added, and the corundum ball in the grinding was stirred( Φ= 1.2 mm) and small ball( Φ= When the volume ratio of 0.8mm) is 0.8:1.5, the medium filling rate is 70%, the grinding mass fraction is 70%, the stripping speed is 800r/min, and the grinding time is 180min, the grinding: be in mineral processing Dice,Plausible(grinding, be in mineral processing) ⋁ Evidence: 0.61. ¬ Typical(grinding, be in mineral processing) Imprint,