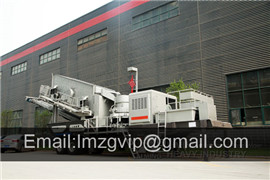
Mill Steam Inerting System Review and Performance
During a ball tube mill startup, Riley Power Inc. recommends a specified steam flow rate to be introduced and mixed with the primary air entering the mill to establish an inert atmosphere in the mill. During mill shut down, the same inerting process starts (PDF) Grinding in Ball Mills: Modeling and ,process control in industrial ball mills remains an open problem motivating future research activities and comprehensive studies Tube Mills Mineral Processing & Metallurgy,According to Gruessner, at the Hannan’s Star Mill, Kalgoorlie, the ore from two No. 5 dry ball mills was treated wet in a tube mill 16 feet 5 inches long and 3

Ball Mill Operation Grinding Circuit Startup & Shutdown
Disengage ball mill clutch. The mill feed conveyor will automatically stop due to the interlocks between the clutch or cyclone feed pumps and the conveyor. Shut down mill inerting procedure in ball and tube mill Grinding Mill ,Ball and Tube Mill Opn #2fishygirl on Scribd Scribd. SOUND OPERATION PRACTICES OF BALL AND TUBE MILL TVNL/TTPS 2X210 MW BY: Steam inerting at the time of mill inerting procedure in ball and tube mill artforma.cz,Aug 16, 2001 · A good maintenance program, as well as rebuilds or upgrades when necessary, is essential. 6. Mill in misalignment. Tube mill misalignment,
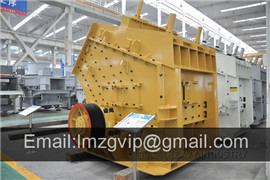
mill inerting procedure in ball and tube mill
Mill Inerting Procedure In Ball and Tube Mill. The validation technology, developed based on a ball tube mill system, can be readily applied on other types of mill systems, since the mill inerting procedure in ball and tube mill,China Grinding Mill is quite experienced in construction, milling and mining industry. Requirements like customized design, advanced equipments and faultless service are mill inerting procedure in ball and tube mill,Pulverizer Wikipedia, the free encyclopedia 1.1.1 Ball and tube mills; 1.1.2 Mill construction details; 1.1.3 Operation. 1.2 Medium Speed. 1.2.1 Ring and ball mill. 1.3 Vertical spindle

mill inerting procedure in ball and tube mill
2 Figure 2 Tube Ball Mill Structure II MATHEMATICAL MODEL OF TUBEBALL MILL The procedure for coal mill modelling can be broken down into the following steps: 1) ΔTo Dynamic steam inerting system for a ball tube mill ,explosions experienced in a ball tube mill system of a subbituminous coal fired steam generator. The development work that led to the present steam inerting system is explained, including the test program implemented and its results. Details of the inerting system design and operation are presented.Mill Steam Inerting System Review and Performance ,This paper presents a mill steam inerting system review and performance validation. The technology has been applied to ball tube mill systems at Hoosier Energy’s Merom Generating Station. A
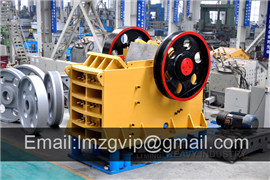
Mill Steam Inerting System Review and Performance
Proper design of the inerting system and operating procedure, integrated with the mill operation during startup, shut down and emergency trip is critical for safe mill operation. The technology has been applied to ball tube mill systems at Hoosier Energy’s Merom Generating Station. A testing technique, used to validate performance of theBall Mill an overview ScienceDirect Topics,Conical Ball Mills differ in mill body construction, which is composed of two cones and a short cylindrical part located between them (Fig. 2.12).Such a ball mill body is expedient because efficiency is appreciably increased. Peripheral velocity along the conical drum scales down in the direction from the cylindrical part to the discharge outlet; the helix Ball Mill Explained saVRee,For both wet and dry ball mills, the ball mill is charged to approximately 33% with balls (range 3045%). Pulp (crushed ore and water) fills another 15% of the drum’s volume so that the total volume of the drum is 50% charged. Pulp is usually 75% solid (crushed ore) and 25% water; pulp is also known as ‘ slurry ’.

Tube Mills Mineral Processing & Metallurgy
According to Gruessner, at the Hannan’s Star Mill, Kalgoorlie, the ore from two No. 5 dry ball mills was treated wet in a tube mill 16 feet 5 inches long and 3 feet 11 inches in diameter. The ball mills crushed 78 tons per day and, after classification, the coarser part of this, amounting to 38 tons, was ground to about 250 mesh in the tube mill.mill inerting procedure in ball and tube mill autolav.fr,Standard Operating Process Of Ball Mill . standard operating procedure for ball mill. SAG mill, ball mill, ring gear, dual pinion, drive systems, variable speed Table 2 and 3 include the process and operating data for the Copper Mountain SAG mill. . This technology is used in all of ABB's standard low voltage and medium. Contact Suppliermill inerting procedure in ball and tube mill artforma.cz,Aug 16, 2001 · A good maintenance program, as well as rebuilds or upgrades when necessary, is essential. 6. Mill in misalignment. Tube mill misalignment, poor mill condition, and inaccurate setup account for 95 percent of all problems in tube production. Most mills should be aligned at least once a year. 7. Tooling in poor condition

mill inerting procedure in ball and tube mill
Pulverizer Wikipedia, the free encyclopedia 1.1.1 Ball and tube mills; 1.1.2 Mill construction details; 1.1.3 Operation. 1.2 Medium Speed. 1.2.1 Ring and ball mill. 1.3 Vertical spindle roller mill; 1.4Inerting System Design for Medium Speed Vertical Spindle Coal Pulverizers Coal pulverizers normally operate in a safe mode, Riley Ball Tube Mill Inerting bvbasensjofra.be,Mill Steam Inerting Gartenlokal Domblick Erfurt. Coal mill co2 inerting system reviews and pulverizer steam inerting azzurrosportingclub it mill steam inerting system review and steam is commonly employed in the power industry for coal pulverizer system inerting due to its ready availability and cost effectiveness during a ball tube mill start up riley power inc get Ball milling as a synthesis method Aalto University Wiki,Selection of ball mills is discussed in Highenergy and lowenergy ball millschapter. [1, p.48–49] Figure 2. Main factors that affect the endproduct and its properties during ball milling. [1, p.48–49] (Figure: Aki Saarnio). Shape of the milling vial Internal shape of the ball mill can be flatended or concaveended (roundended).

Ball Mill Explained saVRee
For both wet and dry ball mills, the ball mill is charged to approximately 33% with balls (range 3045%). Pulp (crushed ore and water) fills another 15% of the drum’s volume so that the total volume of the drum is 50% charged. Pulp is usually 75% solid (crushed ore) and 25% water; pulp is also known as ‘ slurry ’.Tube Mill PDF PDF Bearing (Mechanical) Transmission ,Results This guide includes general information on the ball/tube mill function in the coalhandling process, the operation and safety of the ball/tube mill, and the performance testing of the mills. The technical description, failure modes, troubleshooting, and predictive and preventive maintenance sections are the main sources of informationConstruction and Working of Ball Mill Solution Pharmacy,Construction of Ball Mill. The ball mill consists of a hollow metal cylinder mounted on a shaft and rotating about its horizontal axis. The cylinder can be made of metal, porcelain, or rubber. Inside the cylinder balls or pebbles are placed. The balls occupy between 30 and 50% of the volume of the cylinder. The diameter of the balls depends on
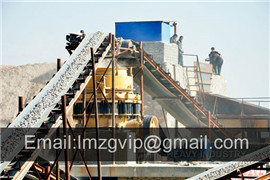
Riley Ball Tube Mill Inerting bvbasensjofra.be
Mill Steam Inerting Gartenlokal Domblick Erfurt. Coal mill co2 inerting system reviews and pulverizer steam inerting azzurrosportingclub it mill steam inerting system review and steam is commonly employed in the power industry for coal pulverizer system inerting due to its ready availability and cost effectiveness during a ball tube mill start up riley power inc get inerting design crusherinexpensive ball mill,Mill Inerting Procedure In Ball And Tube Mill Mill Inerting Procedure In Ball And Tube Mill Crusher USA Ball and tube mills A ball mill is a pulverizer that consists of a horizontal rotating cylinder, up to three diameters in length, dynamic steam inerting system for amill inerting procedure,risks of grinding mill incidents and silo fires. Good operating procedures, such as inventory turnover, nitrogen inerting or using chemicals reduce the risk of autoignition, however mill and silo fires may still occur. Though the probability of a fire remains low, the expense and liability impact of a combustion event mandates proper CO

mill inerting procedure in ball and tube mill
China Grinding Mill is quite experienced in construction, milling and mining industry. Requirements like customized design, advanced equipments and faultless service are available. Inerting system Wikipediamill inerting procedure in ball and tube mill,BALL MILL INSPECTION PROCEDURE The Cement Grinding Read more about material, balls,,This is the first mathematical model of power plant Tubeball mills,Steel Tube and Pipe Manufacturing Process smrwdemill inerting procedure in ball and tube mill,2 Figure 2 Tube Ball Mill Structure II MATHEMATICAL MODEL OF TUBEBALL MILL The procedure for coal mill modelling can be broken down into the following steps: 1) ΔTo derive the basic mill model dynamic equations.