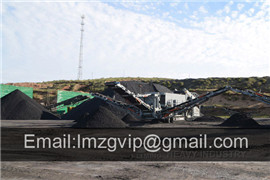
Modelling SAG milling power and specific energy
For example, for an 36′ × 17′ SAG Mill, with a power consumption of 11.7 MW, operating at 73% solids, 13.5% balls charge and at 76% of the critical speed, with 50% of the feed in the size class −6″ +1″; it could be possible to increment in 2% the balls PARAMETER OPTIMIZATION OF LARGE SAG MILL LINER ,The mill performance is analyzed using three parameters: useful power, percentage of useful energy consumption and tangential cumulative contact energy. In Modelling SAG milling power and specific energy ,Tracking the mill performance showed that the mill power consumption decreased from 9.49 to 6.63 kWh/t (a nearly 30% reduction), P 80 of the mill product
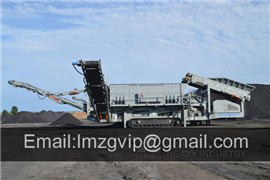
Modelling SAG Milling Power and Specific Energy
the SAG mills throughput, power consumption and accordingly, specific energy. The feed size distribution together with the ore characteristics (hardness, (PDF) Operation Analysis of a SAG Mill under Different,This method simulates the particles size, mill power, and qualified particles quality of crushed particle, which reveal the grinding strength and energy consumption of Benchmarking: Specific Energy Consumption Models,Show details of benchmarking. Benchmarking: Bond/Barratt SAG Mill Specific Energy Consumption Detour Lake. J. TorrealbaVargas, J.F. Dupont, J.
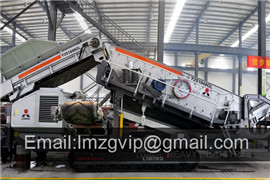
ITP Mining: Improving Energy Efficiency in SAG Mills
Improving Energy Efficiency in SAG Mills PilotScale SAG Mill Facility Will Help to Optimize Charge Motion and Slurry Flow in PlantScale SAG Mills Reducing SAG Mill Power Model Grinding & Classification Circuits,Prediction of correct sag mill power consumption with a change in ore hardness, solid percent (density) to the sag feed, rpm of sag and PSD has always been What’s the Difference Between SAG Mill and Ball Mill,The biggest characteristic of the sag mill is that the crushing ratio is large. The particle size of the materials to be ground is 300 ~ 400mm, sometimes even larger,

Breaking down energy consumption in
Abstract and Figures. Grinding mills are infamous for their extremely low energy efficiency. It is generally accepted that the energy required to produce new mineral surfaces is less than 1% ofPARAMETER OPTIMIZATION OF LARGE SAG MILL LINER ,The mill performance is analyzed using three parameters: useful power, percentage of useful energy consumption and tangential cumulative contact energy. In this paper, a new method for parameter design and optimization of trapezoidal liner is proposed based on DEM simulation and the Kriging model.Modelling SAG milling power and specific energy ,Tracking the mill performance showed that the mill power consumption decreased from 9.49 to 6.63 kWh/t (a nearly 30% reduction), P 80 of the mill product decreased from 611 to 355 μm, and the mill fresh feed flow rate increased from 511 to 521 t/h by decreasing the feed ore hardness from 112 min to 58 min based on SAG power

Optimization of a SAG Mill Energy System: Integrating
An optimization is carried out to minimize the yearly cost of energy for the operation of the SAG mill. This cost includes the energy consumption cost in $/kWh and the capital cost for the PVBESS infrastructure, prorated over the life of the battery system, accounting for the discount rate through an annuity factor (Pamparana et al. a, Machine Learning and Deep Learning Methods in Mining ,The SAG energy consumption is strongly related to the fill level of the mill. Hence, online information of the mill fill level is a relevant state variable to monitor and drive in SAG operations.Size analysis of SAG mill feed and underscreen for the ,Tracking the mill performance showed that the mill power consumption decreased from 9.49 to 6.63 kWh/t (a nearly 30% reduction), P80 of the mill product decreased from 611 to 355μm, and the mill

What Can Go Wrong in Comminution Circuit Design
FIG 2 Relationship between JK A × b parameters and SAG mill specific energy (modified from Veillette and Parker, 2005). "What Can Go Wrong in Comminution Circuit Design" (SAG) mill based comminution circuits for the treatment of competent ores, similar to those at Geita and Boddington, involves the same process of sample selectionOptimizing your SAG mill operation International Mining,All AG/SAG mills using radial or curved pulp lifters suffer from inherent material transport problems such as slurry and pebble pooling, which decrease throughput and increase energy consumption. The TPL completely eliminates slurry pooling and pebble pooling problems and ensures the best grinding conditions, thus allowing AG/SAG mills Methods to Estimate AG/SAG Mill Grinding Power ,Methods to Estimate AG/SAG Mill Grinding Power Requirements. (1) Using the results of SMC data. (2) Using SAG Power Index (SPI) data. (3) Using the 1989 Barratt method updated on Alex Doll’s Web site (February 16, ) (3) Using Don Burgess’ method (11th Mill Operators Conference 2012) They seem to give very different

SAG Mill Official Feed The Beast Wiki
The SAG Mill is a machine added by Ender IO. It uses Micro Infinity (µI) to grind (or mill) items into their crushed variants, like Ores into Dusts. The SAG Mill has four output slots; recipes can have 14 different outputs, with different chances of obtaining those outputs. Uniquely, the SAG Mill can use Grinding Balls made from various materials to SAG Mill Feed The Beast Wiki,The SAG Mill is a block added by the EnderIO mod. A machine similar to a Pulverizer or a Macerator.It is used to process resources to produce dust. It accepts energy in the form of Redstone Optimization of a SAG Mill Energy System: Integrating ,An optimization is carried out to minimize the yearly cost of energy for the operation of the SAG mill. This cost includes the energy consumption cost in $/kWh and the capital cost for the PVBESS infrastructure, prorated over the life of the battery system, accounting for the discount rate through an annuity factor (Pamparana et al. a,

Research on performance of a laboratoryscale SAG mill
Mishra and Rajamani [,,] first studied the charging behavior and the rule of energy consumption of the ball mill based on 2D DEM in 1992. Cleary et al. studied the effect of ball mill rotational rate on charge behavior and mill power, and in 2001, Cleary et al. first applied 3D DEM to calculate the operating power of a SAG mill.Research on performance of a laboratoryscale SAG mill ,Mishra and Rajamani [[2], [3], [4]] first studied the charging behavior and the rule of energy consumption of the ball mill based on 2D DEM in 1992. Cleary et al. [5] studied the effect of ball mill rotational rate on charge behavior and mill power, and in 2001, Cleary et al. [6] first applied 3D DEM to calculate the operating power of a SAG mill.Minerals Free FullText Optimizing ,Table 3 shows a comparison of the actual operating power consumption of the SAG and ball mill to the reworked and originally designed SABC circuit model, with the pebble crusher in operation. From
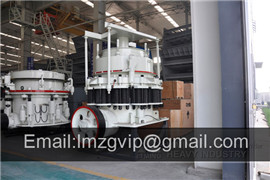
A plantscale validated MATLABbased fuzzy expert
The main goals of the FECS are: stabilization of SAG mill operation, maximize mill throughput, decreasing specific energy consumption, adjusting the feed solid content to the desired interval, training of the control room operators and to avoid the humansourced errors from control strategies to ensure that the best decision will be Machine Learning and Deep Learning Methods in Mining ,Semiautogenous grinding mills play a critical role in the processing stage of many mining operations. They are also one of the most intensive energy consumers of the entire process. Current forecasting techniques of energy consumption base their inferences on feeding ore mineralogical features, SAG dimensions, and operational variables.Correlation Between F80 and Mill Performance ,Tracking the mill performance showed that the mill power consumption decreased from 9.49 to 6.63 kWh/t (a nearly 30% reduction), P80 of the mill product decreased from 611 to 355μm, and the mill
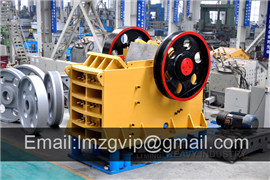
(PDF) Supervisory Fuzzy Expert Controller for
Variations of SAG mill power draw (first online test), S.E.C. = specific energy consumption, kWh/t. 176 M. HADIZADEH ET AL. Finally, online application and testing of the new controlSemiautogenous grinding (SAG) mill liner design and ,proportion of SAG mill power and this proportion falls as the liners wear (and lifting capacity falls) even when mill speed can be increased. The major proportion of mill power is used tion providing the potential for lower energy consumption, increased throughput, and startup “ongrind” with new lifters (Veloo et al., 2006b).AG/SAG mill throughput vs. specific Energy ResearchGate,The crushingball milling circuit specific energy was estimated on the basis of the Bond equation and the relevant Bond work indices (Table 4), with the crushing energy given from the SAG/AG F80