
Separation of lepidolite from hardrock pegmatite ore via
The ore was crushed in a jaw crusher (single toggle 5′’ × 6″, 4 kW, 325–375 rpm, Denver) to produce particles between 20 and 6 mm. and the potential values were below 10 mV. Therefore, it is also evident that separation of these minerals from Mineral processing metallurgy Britannica,mineral processing, art of treating crude ores and mineral products in order to separate the valuable minerals from the waste rock, or gangue. It is the first process that most ores (PDF) ORE SEPARATION BY SCREENING,For example, if a sample of a crushed mineral ore containing 50% by weight of particles sm aller than 1/8” is dropped on a
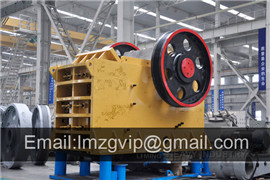
(PDF) ORE SEPARATION BY CLASSIFICATION
Separation is attempted through two methods: i. Screening and ii. Classification. Screening is generally carried out on relatively Different types of separation methods for minerals,This separation can be done either physically, via gravity separation, electrostatic separation and magnetic separation, or chemically, using froth flotation, leaching, and electro Methods to Separate Metal From Ore Geology,Methods for separation of titanium from ore. The grade or concentration of an ore mineral, or metal, as well as its form of occurrence, will directly affect the costs

github
Fruitful separation of minerals from crushed oreSeparation Of Minerals From Crushed Ore pvsm.in Separation Of Minerals From Crushed Ore separation of minerals from crushed separation of minerals from crushed ore,separation of minerals from crushed ore. separation of minerals from crushed ore Effective processing of lowgrade iron ore through separation techniques 571 Ore Crushed Mineral,Ore Crushed Mineral. Separation Of Minerals From Crushed Ore . Crushing equipment for ore mineral processing plant line, ore mineral

separation of minerals from crushed ore Loxicat
Exposure of minerals in crushed ore and metal contents of. 1. From data on the chemical analysis, of ores and concentrates and the values of the constants βmin Preparation of cinnamic hydroxamic acid collector and ,The single mineral flotation test and artificially mixed ore showed that CIHA had an excellent collection effect and selectivity. zeta potential, FTIR, and XPS showed that CIHA was adsorbed on the scheelite surface by strong chemical adsorption. Mineral samples were manually sieved, crushed, and treated with a laboratory ceramic ball millMinerals Free FullText Influence of Water Quality on ,The crushed ore is milled by four autogenous mills and the mill discharge classified using hydrocyclones, Musuku, B.; Dahl, O. Impact of Recycled Process Water on Electrochemical Reactivity of Sulphide Ore. Minerals , 12, 1455. [Google Scholar] J. Physical Separation of Thermally Upgraded Pyrrhotite. Master’s Thesis, Applied

Development of a novel magnetic separator for
The concept of particle separation by rotating magnetic field was proposed by Dean and Devis (Reginald Scott Dean, xxxx; Dean and Davis, 1941).The rotating magnetic field utilized magnetic anisotropy (that depends on exchange forces and crystalline electric fields) and dynamic magnetization response of particles that aid to reduce dependency on Preconcentration of Iron, Rare Earth, and Fluorite from ,Bayan Obo ore contains mainly bastnaesite, monazite and associated iron, fluorite, calcite, dolomite, barite, and trace amount of columbite. Due to its complex mineral compositions and similar mineral properties, it is difficult to separate and obtain rare earth and fluorite concentrates with high purity by conventional magnetic separation and Different types of separation methods for minerals,This separation can be done either physically, via gravity separation, electrostatic separation and magnetic separation, or chemically, using froth flotation, leaching, and electro winning. Unusable minerals, which are often discarded into dams, are called tailing. In order to understand the benefits of dry mineral processing, you must first

Insight into Mineralogy of a LowGrade Manganese Ore
Abstract In this study, the use of XRF, XRD and other instruments found that the manganese content in the ore was 14.53%, and the main forms were carbonate, iron manganese oxide and manganese oxide. Because of the special magnetic susceptibility of these minerals, the magnetic separation method was chosen to improve the grade of Copper Mining and Processing: Processing Copper Ores,After the copper ore is crushed, liquid is added to make it a slurry. The slurry is a mix of valuable copper ore minerals and “worthless” rock, called gangue (pronounced “gang”). The slurry is placed in a tank and a process called froth floatation is used to separate the copper minerals from the gangue. Chemical reagents calledA. Zarrinpour, H. Haghi, M. Jahani Iran’da Fosfat ,The separation of soluble minerals from oxide and silicate minerals has been Phosphate ore is provided at 600 mm size and crushed to 22 mm by two stages
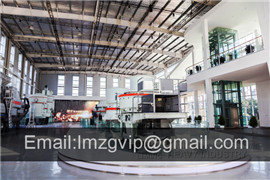
Magnesite Ore Processing: Separation and Calcination
The processing flow is as follows: Step 1 Crushing: Use a jaw crusher, roll crusher, and vibrating screen to form a twostageclosed circuit crushing system to crush the raw magnesite ore to 1mm. Step 2 Calcination: Send the raw ore into a rotary kiln for calcination at a temperature of 700800°C for 1 hour. Step 3 Crushing: Crush the calcinedseparation of minerals from crushed ore Loxicat,Exposure of minerals in crushed ore and metal contents of. 1. From data on the chemical analysis, of ores and concentrates and the values of the constants βmin and τ for nonmetalliferous minerals the authors have determined the exposure of the minerals being extracted in the original crushed ore and have calculted the content of metal Preparation of cinnamic hydroxamic acid collector and ,The single mineral flotation test and artificially mixed ore showed that CIHA had an excellent collection effect and selectivity. zeta potential, FTIR, and XPS showed that CIHA was adsorbed on the scheelite surface by strong chemical adsorption. Mineral samples were manually sieved, crushed, and treated with a laboratory ceramic ball mill

Minerals Free FullText Influence of Water Quality on
The crushed ore is milled by four autogenous mills and the mill discharge classified using hydrocyclones, Musuku, B.; Dahl, O. Impact of Recycled Process Water on Electrochemical Reactivity of Sulphide Ore. Minerals , 12, 1455. [Google Scholar] J. Physical Separation of Thermally Upgraded Pyrrhotite. Master’s Thesis, AppliedPreconcentration of Iron, Rare Earth, and Fluorite from ,Bayan Obo ore contains mainly bastnaesite, monazite and associated iron, fluorite, calcite, dolomite, barite, and trace amount of columbite. Due to its complex mineral compositions and similar mineral properties, it is difficult to separate and obtain rare earth and fluorite concentrates with high purity by conventional magnetic separation and Development of a novel magnetic separator for ,The concept of particle separation by rotating magnetic field was proposed by Dean and Devis (Reginald Scott Dean, xxxx; Dean and Davis, 1941).The rotating magnetic field utilized magnetic anisotropy (that depends on exchange forces and crystalline electric fields) and dynamic magnetization response of particles that aid to reduce dependency on

Minerals Special Issue : Mineral Liberation MDPI
In addition, knowing what minerals accompany the ore is necessary for applying separation techniques. This Special Issue aims to provide a compilation of the latest advances on mineral liberation. This Minerals Free FullText Extraction of Nickel from ,In this study, segregation roasting and magnetic separation are used to extract nickel from a garnierite laterite ore. The garnierite laterite ore containing 0.72% Ni, 0.029% Co, 8.65% Fe, 29.66% MgO, and 37.86% SiO2 was collected in the Mojiang area of China. Garnierite was the Nibearing mineral; the other main minerals were potash A. Zarrinpour, H. Haghi, M. Jahani Iran’da Fosfat ,The separation of soluble minerals from oxide and silicate minerals has been Phosphate ore is provided at 600 mm size and crushed to 22 mm by two stages

Magnesite Ore Processing: Separation and Calcination
The processing flow is as follows: Step 1 Crushing: Use a jaw crusher, roll crusher, and vibrating screen to form a twostageclosed circuit crushing system to crush the raw magnesite ore to 1mm. Step 2 Calcination: Send the raw ore into a rotary kiln for calcination at a temperature of 700800°C for 1 hour. Step 3 Crushing: Crush the calcinedMethods of concentration of Ores Gravity Separation.,Also known as enrichment, the concentration of ores is the method of removing impurities and other unwanted particles from the ore. The removal method of the gangue particles or the unwanted particles depends on the difference in physical or chemical properties of the ore and the impurities. The minerals present in ores are found in the How To Separate The Different Mineral Components Of ,In quartz ore beneficiation, the separation of different mineral components and quartz has a great influence on the purity of quartz concentrate. The common mineral components in quartz ore include mica, feldspar, ironbearing minerals, and apatite. The following sections describe how the common mineral components of quartz are